Apr 30, 2021
Retrofitting Manufactured Homes—Part 1
By: Bob Pfeiffer
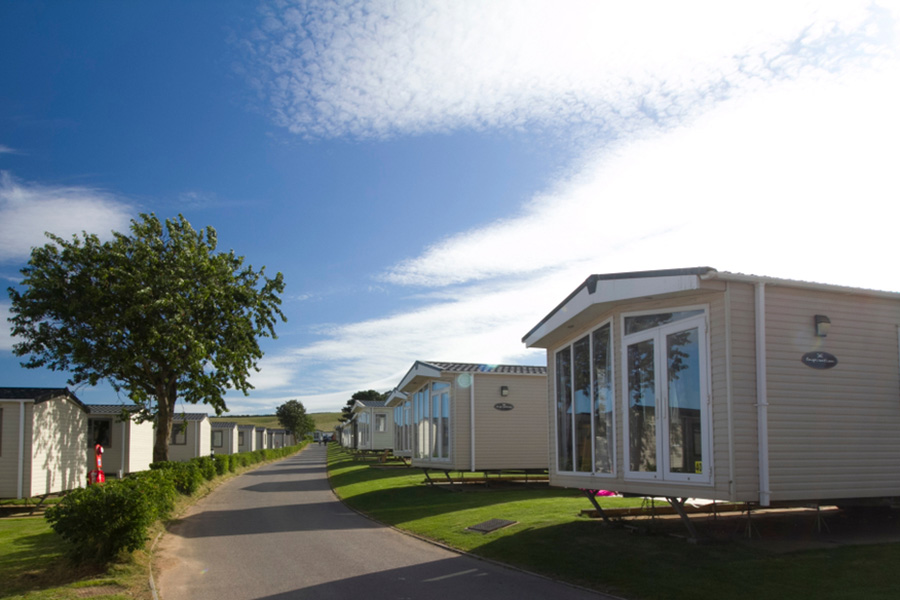
If there is one housing style in America that immediately conjures up a wide range of imagery, it’s the mobile home. Maybe you have a snarky movie or TV scene in mind, a story, or an opinion about mobile homes. But do you see mobile home retrofitting as an opportunity?
(Note that the term mobile home applies to any manufactured home built prior to June 1976, before U.S. Department of Housing and Urban Development policies changed. They have since been replaced by modern manufactured homes.)
Manufactured homes are home for millions of Americans; they fill a key role in housing our fellow citizens. They provide an affordable option for some of our most vulnerable neighbors in a country where the cost of housing challenges many families. Many energy retrofitters may not understand the special issues associated with these homes, but thankfully, building science professionals possess the tools and knowledge to significantly improve performance, indoor air quality, and safety of these units.
And we can make a meaningful difference for the people who live in manufactured homes.
Distribution Systems
This article will tackle key components of the typical distribution system, as opposed to just the ductwork. I will share some strategies for building performance professionals who may be operating duct-sealing retrofit programs where whole-house measures cannot be implemented. I will mostly address heating loads, but these factors also apply to cooling loads. In addition, I’ll challenge our industry to consider the unintended consequences of our craft and the programs design—especially in light of climate change and the kind of severe weather events we never imagined.
Duct Sealing and Freezing Pipes
If we want to create efficient, safe, and durable living conditions for our clients, we have to deal with some physical realities unique to mobile homes.
Duct sealing can’t be performed in a vacuum. We must assess the condition of the road barrier and the completeness of the insulation. Damaged road barriers are susceptible to freezing water lines; in fact, it is not uncommon to observe holes in the ductwork that someone added intentionally to keep pipes from freezing.
As ductwork is sealed, less conditioned air escapes into the floor cavity, which in turn lowers the floor cavity temperature. How much lower? That depends on the condition of the road barrier and existing weather conditions.
Our goal is to seal leaky ductwork, but we don’t want to create conditions that cause pipes to freeze.
Program designers must factor this in—especially considering the increase of extreme weather events like this year’s polar vortex effects as far south as Texas. All stakeholders, either designing, implementing, or performing duct sealing programs must consider adding robust road barrier repair and insulation, coupled with waterline insulation strategies to protect the residents of manufactured housing from unintended consequences.
Any reduction of designed airflows in the distribution system can cause stress to be placed on the heat exchanger in winter and cause icing of air conditioning coils in the summer. We must assure our work and homeowners actions facilitate optimal operation of the system.
10 Key Areas For Optimal Operation
I’ve identified 10 key areas that must be inspected, tested, treated, and verified for the distribution system to operate optimally.
We will start with the conditioned air emanating from the furnace
- Air-conditioning coil
- The fins can capture dust and debris, causing poor airflow. This can cause a high temperature rise in winter and icing coils in the summer.
- Access is gained by removing the vertical plates at base of the furnace.
- Inspect both front and back sides.
- Carefully vacuum or brush dust away without crimping the fins.
- Check condensate pan for cracks and proper drainage.
- Clean the condensate pan and drain line as necessary.
- Inspect bottom side of heat-exchanger with mirror for cracks, wear, etc.
- Plenum/base
- Not accessible from the furnace when A-coil is present, which means it must be accessed from under the trailer, which is difficult at best.
- Use a pressure pan test (addressed later) to determine if leaks emanate from this location as this may be one of the largest sources of duct leakage.
- If possible, perform visual inspection via register closest to the plenum to verify condition
- If indicated, suit-up, crawl under there, and get to work!
- Assure all patches will be durable- use mechanical fasteners and redundant sealing techniques.
- Insulate under ductwork and repair road barrier upon completion.
- Trunkline, crossover (for double-wide mobile homes)
- Crossovers are notoriously compromised and should always be inspected, regardless of test results. Water and animal damage are frequent since, in many cases, these components are exposed.
- When accessible, I use a flashlight and mirror or a digital camera to inspect the lines. It’s also very important to inspect the trunk-end cap, as it is a weak spot.
- Trunk leaks can be treated from under the unit if the road barrier is compromised.
- If you have to slice through the road barrier at any point, it is imperative to repair it with a patch that is durable . We recommend the “sling patch” for work between the I-beams, and 1 in. foam board under branch ducts and water lines.
- Boots/collar/riser
- This is the first location most technicians consider because it is easily accessible, and usually shows signs of deterioration. Perform trunkline inspection at this time.
- Follow well-documented protocols for sealing and securing this component. (Here’s a video from Cal Steiner that is useful.)
- Registers
- Replace crushed or flattened grills with non-closing, non-restrictive models to maximize air flow.
- In some cases, repair of the riser will decrease the effective opening size, making it impossible to set the existing register in place without damage to the work. In this case, use a zero-profile register.
- Assure belongings or furnishings do not inhibit air flow.
- Room pressurization (this will be performed after all work is completed)
- Energize the air handler and check each closeable room for pressure differential in relation to main body of the house.
- No room with a closeable door should pressurize above 3 Pascals with door closed.
- If there’s a differential >3 Pascals, we recommend adding a grille to the door, or some other means to alleviate positive pressure in that room. Sound attenuation must be considered.
- Furnace closet combustion appliance zone (CAZ) door (if present)
- Note that these specifications may vary across different jurisdictions and programs.
- Closet installations must use a louvered door having a minimum free area of 235 sq.in. when located ≥6” from furnace.
- For clearance between 1” and 6” from furnace, requirements are a louvered door with minimum of 235 sq. in. free area, with the openings in closet door directly inline with the louvered openings in the furnace door.
- For 1” clearance from furnace, use a fully louvered door with at least 400 sq. in. of free airflow area.
- With air handler operating, CAZ door should not offer significant resistance when opening.
- Furnace filter
- Filters must fit tightly
- Clean or replace- Instruct homeowner to monitor filter and furnace door condition frequently to maintain good airflow through the system.
- Furnace Closet
- If furnace is in a compartment (CAZ), this space is under strong negative pressure and must be considered part of the return side of the system.
- Seal all gaps or holes around the chimney, ceiling, exterior walls, fresh-air intake, and floor. (See the photo below. This pathway into the attic cavity is a major leak in the distribution system.)
- Air handler/blower/fresh-air intake
- Fins should be clean and free-moving.
- If you remove it from the furnace to clean it, perform a visual inspection of the heat exchanger.
- Clean fresh-air supply intake filter if present, and determine if powered damper is operational.
This is the first of three installments.