Jul 18, 2025
The Modular Solution to America’s Building Crisis
The nationwide building crisis—along with rising construction expenses—has triggered a quiet industrial transformation in factories.
By: Adepeju Nafisat Sanusi
Freddie Mac indicates that the United States faces a housing deficit of more than 3.2 million units. That means there are not enough homes available to meet the demand of the population, particularly in relation to affordability.
This nationwide building crisis—along with rising construction expenses—has triggered a quiet industrial transformation in factories. Modular construction is gaining momentum because of modern technological progress, immediate construction needs, and rising popularity for quick, cost-effective, sustainable housing solutions.
Traditional construction is limited by high labor expenses, supply chain problems, and declining skilled workforce numbers. Modular construction presents itself as a required evolution that combines scalability and cost-effectiveness to address current needs.
The modular construction process, which manufactures building parts outside the site before assembly on-site, has existed for a long time. Modern modular construction represents an entirely different approach from previous prefab homes.
Modern advancements in automation systems, digital design methods, and supply chain logistics systems have driven sector-wide changes. The quality standards and performance capabilities of contemporary modular structures match, and sometimes surpass, those of traditional on-site built properties.
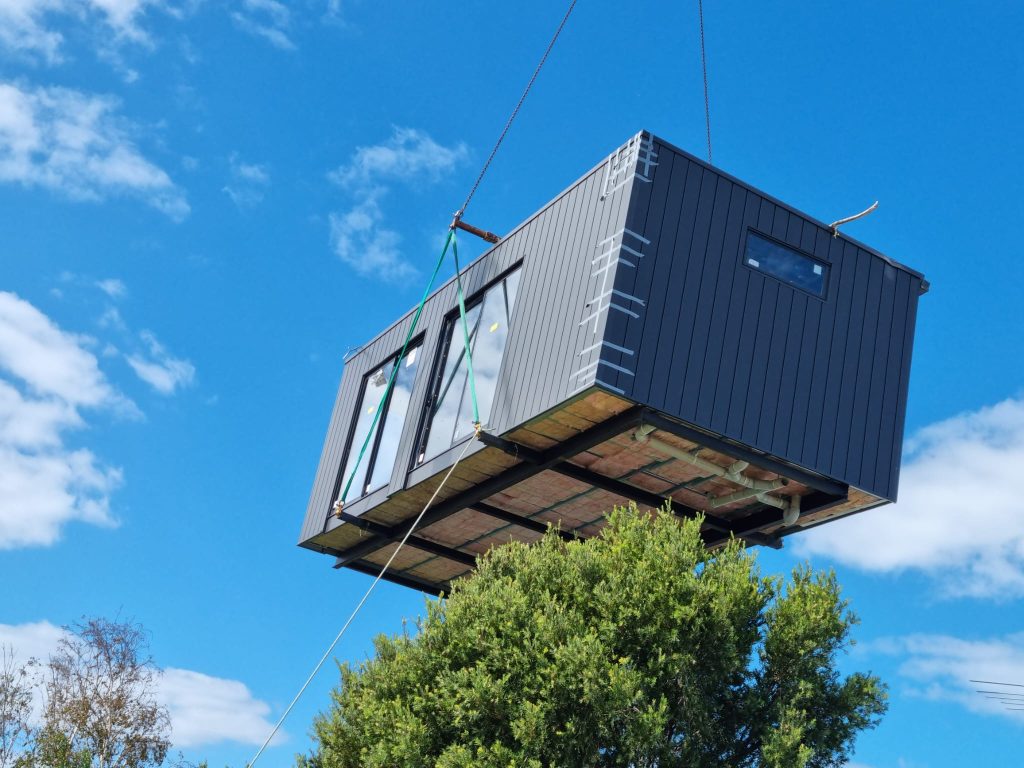
Benefits
Time Savings
The transformative nature of modular construction stems mainly from its accelerated pace. The modular construction process operates in parallel streams that allows projects to finish within half the duration required for traditional methods, since foundation preparation occurs on-site and manufacturing occurs in factory facilities. The fast-paced modular construction process creates a significant advantage for developers in dense urban areas where delayed construction leads to significant daily expenses.
Efficiency
The benefits of modular construction extend beyond its time-saving attributes. The efficiency of the construction process improves significantly while environmental performance experiences significant enhancements. The indoor build process reduces material waste by 90% and enhances quality control while eliminating all weather-related delays. The modular construction approach increases workplace safety and delivers predictable results that help developers reach challenging environmental and regulatory requirements.

From Major Development to Residential Impact
Major developers have already demonstrated their commitment to this potential. Through modular construction, Marriott International aimed to develop 13% of its North American hotel properties. The company launched a 26-story modular hotel development in New York City in 2021, one of the tallest modular structures ever constructed. The modular construction method enabled the fabrication of complete hotel rooms, including furniture, which were later placed at the site using cranes, resulting in reduced construction duration and less disturbance to the neighborhood while saving expenses.
The technological advancements within the industry are transforming the creation of affordable housing. At the same time, this sector faces an urgent need for new solutions. Los-Angeles and Seattle have started using modular solutions to develop new homeless housing and address declining middle-income housing availability.
Vallejo-based Factory-OS works with public institutions and technology companies to create high-quality housing units through rapid and large-scale production. The company achieved an unprecedented goal of building more than 1,000 units during 2022 through its modern manufacturing process.
Residential housing is a key success area, with contractors driving the shift toward accessible, energy-efficient homes. Modular construction offers a practical, scalable solution for both public and private sectors. The National Renewable Energy Laboratory (NREL) highlights modular innovation as a way to deliver affordable, energy-efficient homes nationwide. These advances create new opportunities for contractors to lead sustainable homebuilding at all levels.
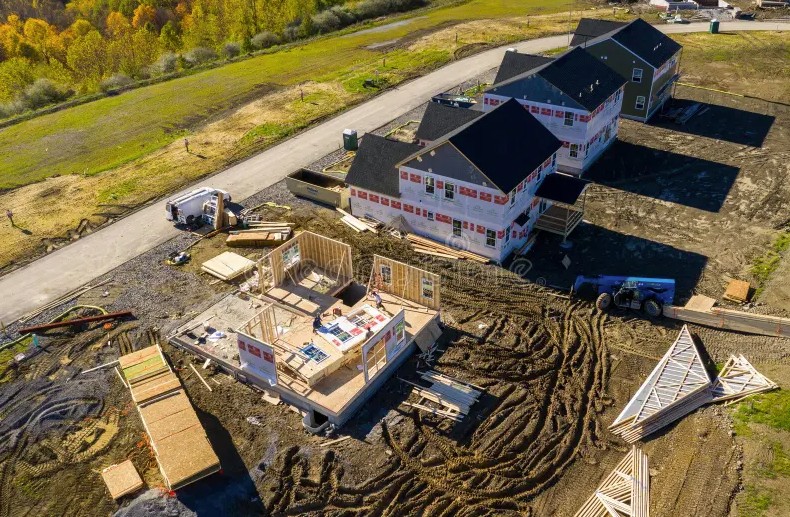
Barriers
Still, barriers remain. The challenge with financing continues because banks and insurers need specific frameworks to understand the unique risks of modular construction. Many state and local building codes were written for traditional construction methods, which fail to accommodate modular construction. The general public maintains incorrect beliefs about modular construction because they associate it with poor-quality mobile homes, even though current designs have achieved significant improvements in both quality and appearance.
These obstacles do not represent impossible hurdles to overcome. Modular construction success stories combined with increased awareness have transformed public skepticism into widespread confidence. The global supply chain vulnerabilities exposed by COVID-19 and the demand for local infrastructure development created rapid growth in the modular construction industry. Factories can rapidly construct hospitals with dormitories and multifamily residential units, which proved essential during the public health crisis.
A Way Forward
The most convincing aspect of modular construction is how well it aligns with nationwide objectives. Modular construction enables the United States to achieve two critical national goals by restoring manufacturing operations and creating significant economic emission reductions. The built environment produces approximately 39% of global CO₂ emissions, which demands new construction approaches to reverse climate change.
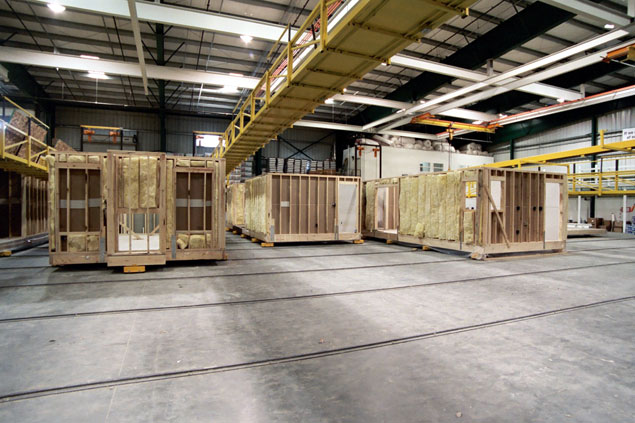
Organizations that adapt their operations quickly will become the future winners in this market. Policymakers need to modernize zoning laws and building codes to accept off-site construction methods. Financial institutions’ underwriting models require revision to show the minimized risk profile and shortened construction duration of modular construction. The development industry must remove outdated thoughts about modular construction boundaries because speed, sustainability, and aesthetics no longer exist as separate elements.
For contractors working directly in homes—particularly market rate and WAP contractors—this shift presents an exciting opportunity to expand skills and enhance their role in the construction process. By embracing new workflows and partnering closely with modular manufacturers, contractors can streamline their work, reduce on-site delays, and focus more on high-value tasks such as installation, finishing, and customization of modular components.
Rather than diminishing their role, modular construction opens doors to greater efficiency, improved quality control, and faster project delivery. Contractors who adapt will not only stay competitive but also become essential contributors to a more sustainable, innovative, and profitable residential construction market.
The modular revolution has already arrived. Modular construction has changed the building process, enabling us to achieve things that previously seemed impossible.