May 28, 2024
Construction Technologies Aiding in Energy Efficiency Efforts
Sustainable construction methods require more than just smarter materials and supplies.
By: Evelyn Long
True energy efficiency must be a concern throughout a construction project, whether commercial or residential. Climate changes, rising costs, and resource deficiencies mean society must make a conscious effort to be better. Energy efficiency is one facet of that, and it involves keeping down consumption and related costs, and reducing waste through more intelligently designed builds.
Energy-efficient homes use less energy through development and design improvements. That’s precisely the idea behind the current evolution of the construction industry, with many new and innovative technologies directly aiding efficiency efforts. Here are a few that are making a difference.
1. Building Information Modeling
Pros
- An eco-conscious design and planning tool
- Interoperability with additional construction tools
- Fewer project reworks or physical errors
Cons
- Requires an expensive initial investment
- Staff need to be trained in using the software
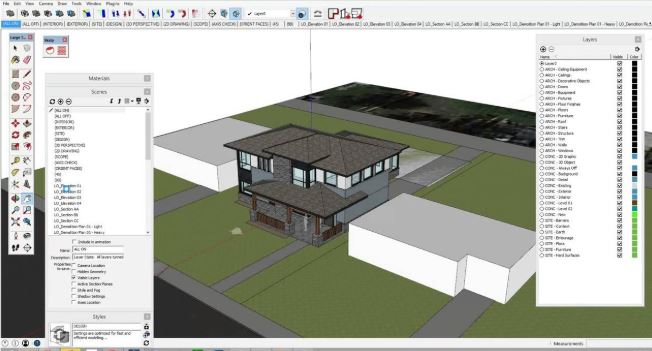
Sustainable construction methods require more than just smarter materials and supplies. Sustainability requires being environmentally conscious in everything a crew does. Every step matters, from the insulation used to seal a building to the installed windows and doors. Even the orientation of a property and how much sun it’s exposed to during the day makes a difference. Building information modeling (BIM) technology can help economically and environmentally.
A project that uses BIM from the start inherently accounts for energy efficiency and takes several steps to improve it. The technology is specifically designed to help achieve more efficient solutions and interoperability. It aids in identifying power-saving opportunities, helps analyze builds and the materials used, and integrates with other software tools — like building automation systems (BAS) — to optimize operations when a project is underway.
2. Enhanced Telematics
Pros
- Better overall efficiency and productivity
- Reduced operational costs
- Empowers excellent automation opportunities
Cons
- Requires robust data and analytics support
- No one-size-fits-all solution
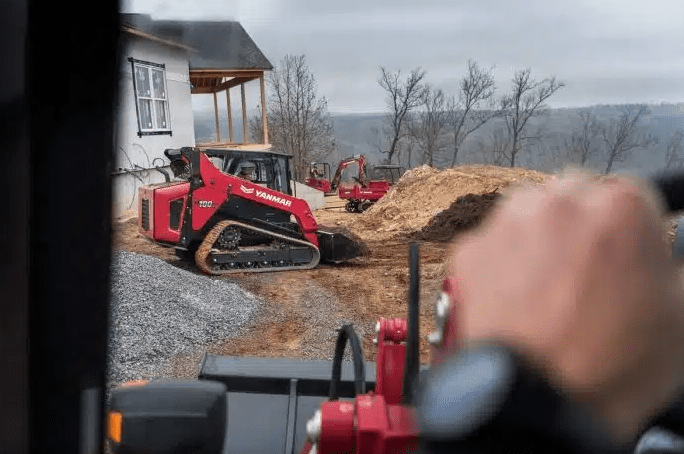
Heavy machinery and equipment on the job site also affect overall efficiency. For example, emissions, fuel consumption and miles traveled are just a few concerns. Enhanced telematics powered by onboard sensors vastly improves their operation by tracking performance in near real-time, logging and reporting data, and assisting with command operations and organization. Think of it as a dashboard that provides oversight into a construction fleet’s complete movements without being on-site.
Crucial data points that can be tracked are load information, vehicle inspection status, total hours used, fuel consumption, driving habits, idle times, and machine alerts. The technology provides granular insights into the construction project, which can inform performance-driven actions and decisions. Operators can remove inefficient or malfunctioning machines from the playing field. Active efforts can occur to reduce equipment fuel consumption by shortening travel times, reducing idle periods, scheduling proper maintenance, and optimizing load sizes during transport.
3. Built-in Smart Tech
Pros
- IoT and smart devices incorporated from an early stage
- Many cost savings and efficiency improvements
Cons
- They require data monitoring and support systems like a smart hub.
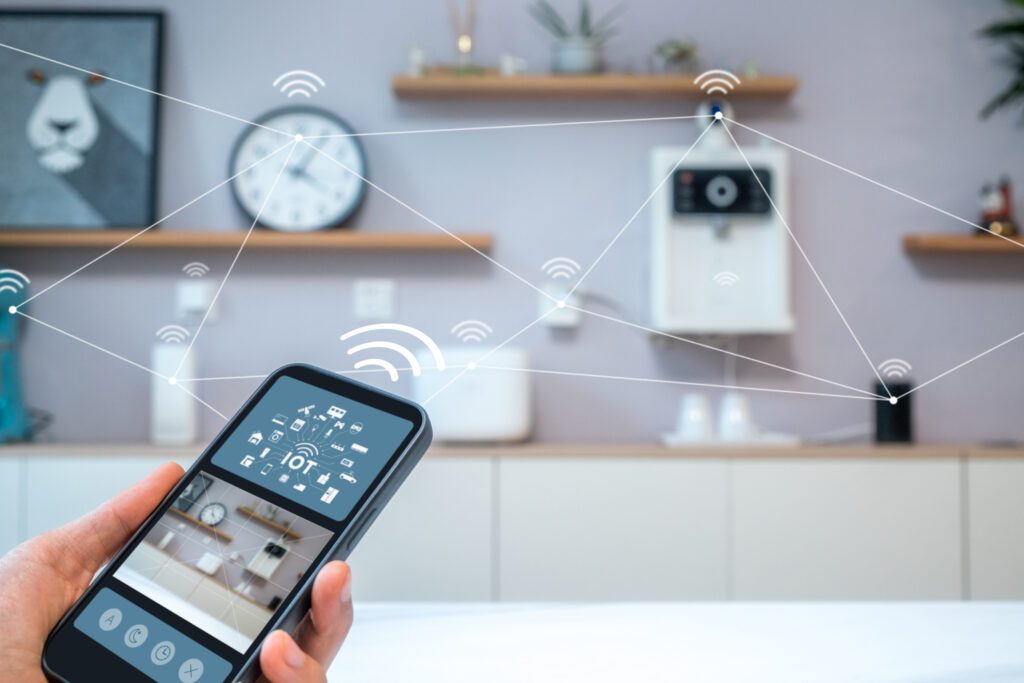
Typically, homes are built to homeowners, architects, and property planners’ cost and design specifications. The base build may not include certain amenities like smart lighting, smart HVAC, or the Internet of Things (IoT). But with modern construction, these solutions can be installed from the get-go, sometimes incorporating the foundations of a structure. For example, flood and water leak sensors could be built into the plumbing, or IoT sensors could adjust blinds based on incoming sunlight or turn off lighting in unoccupied rooms.
Many of these solutions also empower automation, further boosting efficiency in a home or property. The previous IoT sensor example of adjusting the blinds would ultimately lower cooling costs by reducing the amount of sunlight and heat entering the house. Over time, the simple act of closing the blinds nets substantial cost savings for the homeowner but also lowers energy usage, especially for HVAC systems. This technology could vastly improve operations in commercial structures, especially with varied tenants.
4. 3D Printing
Pros
- Everything can be printed on location
- Reduced transport and travel costs
- Diverse material selection, including concrete, wood, and metal
Cons
- Materials are still needed and must be on-site
- The initial technology investment is expensive
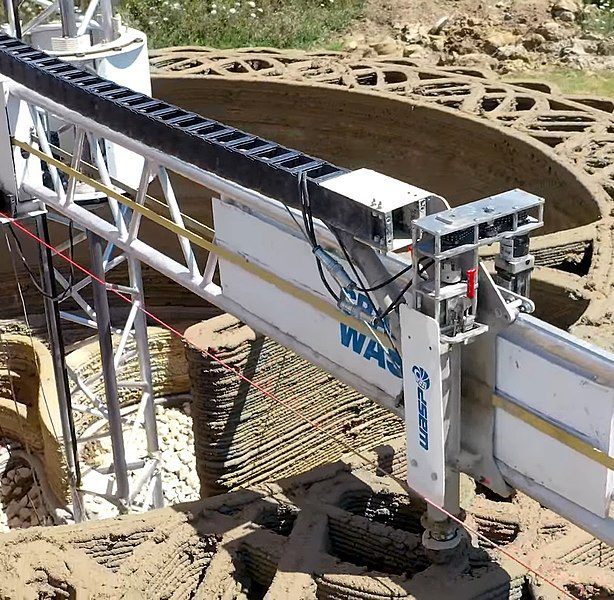
Construction materials are costly, and that’s excluding transport costs. In many cases, builds must be assembled on-site, calling for additional materials — take concrete, for example. Concrete is poured using rebar, wood, and other structural elements to help form and support the finished segment. A steady supply of concrete is necessary to complete a pour, but so are the additional materials. Nearly all these requirements can be limited by using modern 3D printing.
With 3D printing, the materials and the printer are often transported to the site. Then, the hardware creates the necessary parts, components and building segments. There’s no need for repeated travel — everything can be done on-site, anywhere. It dramatically reduces the associated costs, reduces the dependence on large equipment and thereby scales down the carbon footprint of the construction operation. It’s so effective that a large 3D printer can craft a concrete house from scratch in less than 24 hours.
The Technology Making Construction’s Future Brighter
Technology can help improve construction’s ecological impact and energy efficiency. It reduces consumption, allowing better use of available resources. It also helps empower thoughtful operations while building new homes and properties.
That is precisely what many of the technologies here provide. From BIM modeling for efficient design to 3D printing for on-site assembly and enhanced telematics for optimal use of heavy machinery, it all plays a role in creating a brighter, more eco-friendly future.