Jan 4, 2023
Single-Point vs. Multi-point Blower Door Testing
The main purpose of a blower door test is to confirm the integrity and continuity of a building’s air control layer or air barrier. Randy Williams has a few options for how to perform the test; the one he chooses depends on the reasons for performing the test:
By: Randy Williams
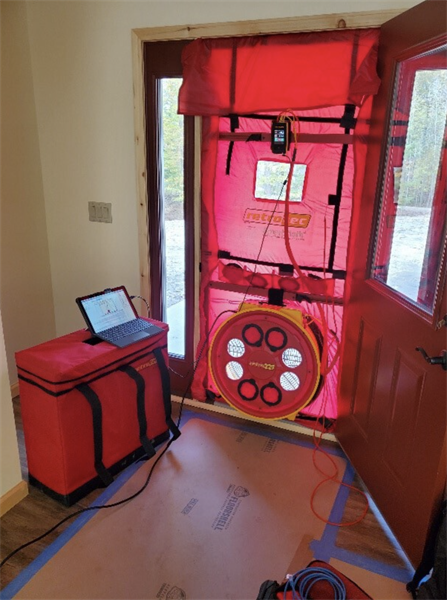
The main purpose of a blower door test is to confirm the integrity and continuity of a building’s air control layer or air barrier. I have a few options for how to perform the test; the one I choose depends on the reasons for performing the test:
- Testing to verify code compliance.
- Testing as part of an energy audit.
- Testing before, during, and after a renovation or remodeling project.
- Testing during a new build.
- Using the blower door to assist air-sealing.
In the case of a code-compliance test or an energy audit, I want the most accurate test I can perform. Accuracy typically improves when more data is included in the test. If we are simply looking for holes to seal in an existing home, though, I may not need lots of data; I just need to run the blower door to help find the holes. The conditions will dictate whether I use a single-point test or multi-point test—or just set the fan to operate on cruise control to hold a constant pressure to identify air-leak locations.
How a Blower Door Operates
Before we get into single-point and multi-point tests, let’s review how a blower door operates. A blower door is designed to move air into or out of a structure through a calibrated fan. In residential construction, we induce a pressure difference of 50 pascals, or 0.2 inches of water column, between inside and outside the building. A manometer or pressure gauge is used with the fan to measure the amount of airflow moving across the fan. This airflow matches the airflow of the leaks in the building at the pressure of 50 pascals (the actual measurement details are little more complicated than this description, but this is basically how it works).
In the United States, airflow is measured in cubic feet per minute, or cfm. The airflow measurement can also be used along with the building volume or square footage to calculate other airtightness metrics, such as air exchanges per hour (ACH) or cfm of airflow per square foot of surface area.
The accuracy of the airflow measurement is dependent on several factors, including equipment accuracy and condition, wind fluctuations, and temperature differences between inside and outside the building. The accuracy (or measurement uncertainty) can be improved when more data is collected during the test.
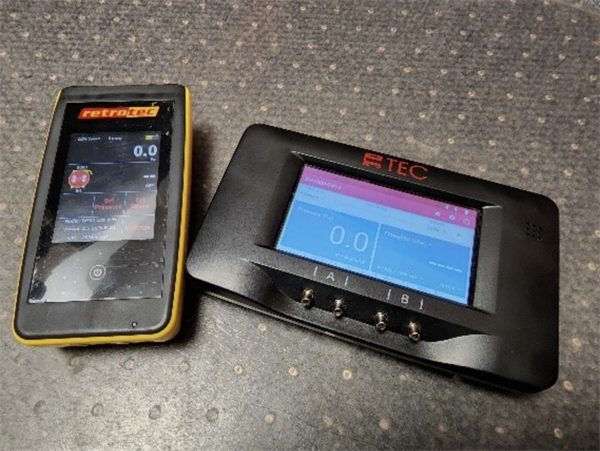
How Data Is Collected
Data collection during a blower door test is most accurate if the process is automated. Blower-door manufacturers have software for quickly and precisely running a blower door test. For operating the software, smartphones, tablets, and laptops are all good choices; I use a Microsoft Surface Pro but have also used a Samsung phone and a standard laptop to perform testing. The choice of using a phone, tablet, or laptop may be limited by the pressure gauge or manometer used. The newer DG-1000 from the Energy Conservatory and the DM32 from Retrotec can communicate with a computer by a hardwire connection or wirelessly (see photos above). Some manometers may need additional components to connect to some devices. Older manometers, such as the one pictured below, are analog and require measurements to be collected manually.
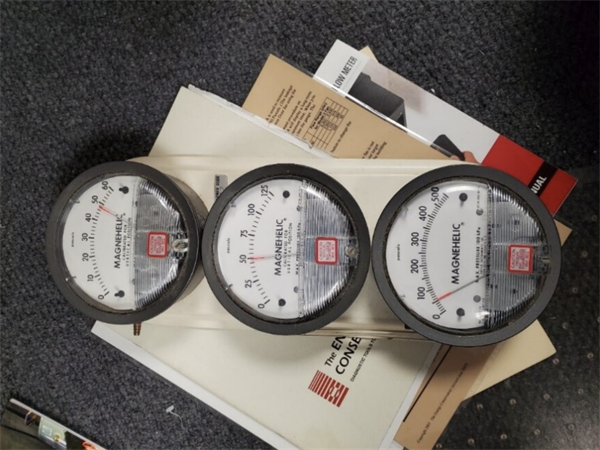
Single-Point Test
For a single-point test, we collect the airflow data (in cfm) at only one pressure point, typically 50 pascals. When we’re testing using the ANSI/RESNET/ICC 380-2019 standard, the measurement of airflow moving across the fan is averaged over at least a 10-second time period. Simply put, the fan holds a steady 50 pascals of pressure difference between inside and outside the structure while the airflow across the fan is measured for 10 seconds. The data points collected over those 10 seconds are then averaged to arrive at the final airflow measurement.
It is possible to adjust the time period for collecting the data; in fact, there may be situations in which you want to collect data over a longer period. If it’s windy, for example, increasing the period from the minimum 10 seconds to 30, or even 60, seconds will help improve the accuracy of your results.
There are variations to a single-point test. A repeated single-point test is what it sounds like: Several individual single-point tests are performed, then the results are averaged. Another variation is to perform the single-point test in both directions, pressurized and depressurized, and average those results. Again, more data equates to more accurate results.
When you’re performing a single-point blower door test to the ANSI/RESNET/ICC 380 standard (which is used for both a HERS rating and code-compliant testing), a 10% adjustment needs to be added to the final number to meet the requirement.
Multi-Point Test
A multi-point blower door test is conducted at several different pressure points. The ANSI/RESNET/ICC 380-2019 standard requires testing at a minimum of five different pascals of pressure between 10 pascals and 60 pascals. The airflow data is collected over a minimum of 10 seconds at each of the pressure intervals.
Manufacturers make software designed to perform these tests to the required standard; for example, The Energy Conservatory’s Auto Test software (which currently operates only on phones and tablets) has several multi-point test options. One of the options is the RESNET 380 multi-point test mentioned above. For that test, the pressure points are 60 Pa, 48 Pa, 35 Pa, 23 Pa, and 10 Pa. Another option in the software is the ASTM E779 multi-point test (another testing standard allowed by the IRC). There are eight different pressure points in this automated test: 60 Pa, 54 Pa, 48 Pa, 42 Pa, 36 Pa, 30 Pa, 24 Pa, and 18 Pa.
One reason for conducting a multi-point test is that it is more accurate for predicting building leakage at lower pressures. During normal operating conditions, a typical home rarely sees 50 pascals of pressure difference between inside and outside. More commonly, the pressure difference will be under 10 pascals. To predict the leakage rate at lower pressures, a building leakage curve is produced after a multi-point test is completed (see graph, above). Though the building leakage curve can be estimated using a single-point blower door test, the curve is more reliable when a multi-point test is used.
The test performed in the example above was an ASTM E779 multi-point test. The leakage rate at 60 pascals was 806 cfm, and at 18 pascals, 339 cfm. The curve shows us the predicted leakage rates down to a difference of 4 pascals of pressure.
What happens if you are unable to reach at least 50 pascals of pressure during multi-point testing? The 380 standard will allow a multi-point test to be used as long as at least 25 pascals of pressure can be reached. Less than 25 pascals and the test is required to be a single-point test. Most current software options will convert the test results when a “can’t reach 50” test occurs.
Returning to the point that more data means more accuracy, both single-point and multi-point blower door test results are only as good as the information provided for the calculations. If you are conducting a test during the winter in a very cold climate, you will need to account for the difference in temperature between inside and outside the home, or if you live in a mountainous area, elevation needs to be accounted for. Another important piece of information is the baseline pressure (normal difference in pressure between inside and outside the building). When you’re performing an automated test using software, the software will perform a quick baseline test and automatically adjust the fan speed to account for the pressure difference. When performing a manual test, you will need to do the calculations by hand and make the adjustments manually.
There are many reasons to perform a blower door test. Sometimes we want to perform the most accurate test we can; other times we just need to run the blower door to help us find the holes. Having a basic understanding of the differences between a single-point and multi-point test can help you decide which test to perform. The only time I perform single-point testing is to confirm the leakage rate of a structure before setting the fan on cruise control to find the air leaks. In all other situations, I perform multi-point tests.
This article was originally published in The Journal of Light Construction and is republished with permission.
Earn CEUs
Earning CEUs on the BPA Journal is a member-exclusive benefit. Please log in to complete the quiz and earn them or join as a member today.