Mar 17, 2023
Frost-Protected Shallow Foundations
The biggest benefit of FPSFs is the reduced cost over other foundation systems. Affordability in new construction over the past couple of years has been an issue, so cost-savings with a reliable end-product can make this system a good choice.
By: Randy Williams
What the building codes say about this cost-saving alternative to conventional concrete foundations
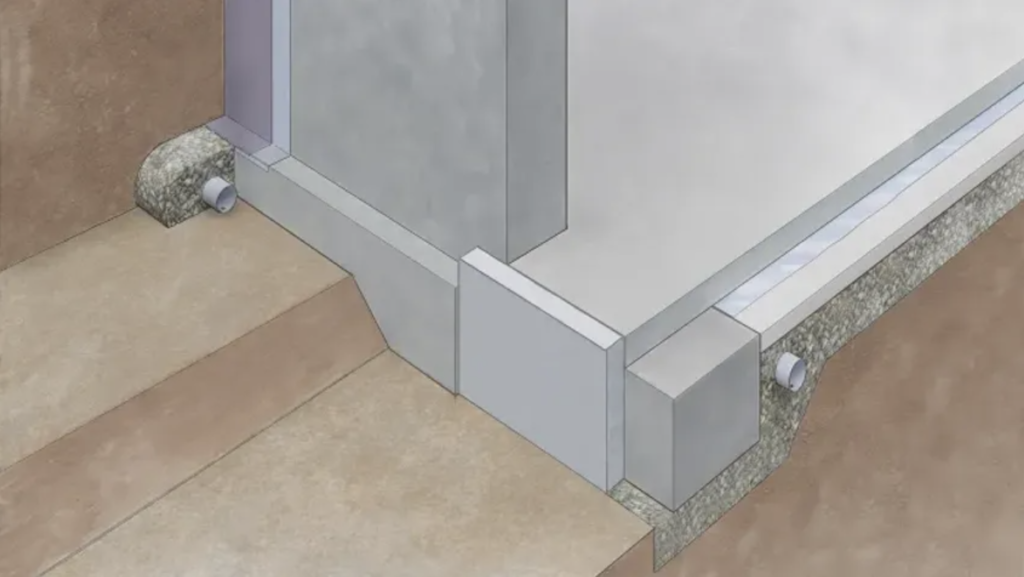
One of the most popular foundation systems used in my Minnesota market (climate zone 7), and one I’ve been using for more than a decade, is the frost-protected shallow foundation (FPSF). In part, that’s because code requires footing depths of 5 ft.; and digging, constructing, and insulating footings and a foundation system that deep is time-consuming and expensive. A shallow-foundation system can be a substantial saving for a new build.
The International Residential Code (IRC) covers FPSFs in section R403.3. There is a lot of information specific to this type of foundation that differs from other systems. For instance, when using an FPSF, the average mean temperature of the building needs to be maintained at a minimum of 64°F (there are ways to design a frost-protected foundation for unheated and semi-heated buildings, but this article will concentrate on continually conditioned dwellings). There are also requirements for rigid insulation R-value derating and protection for buried insulation.
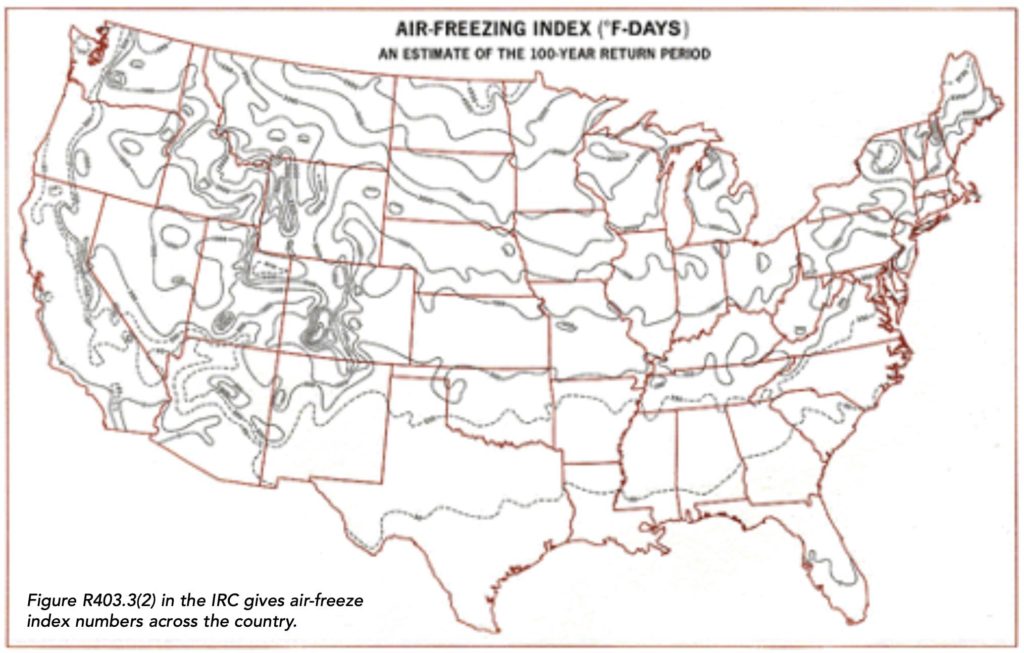
What is an FPSF?
A frost-protected shallow foundation system is typically a monolithic concrete pour, sometimes called a turned-down slab, where the footing and slab are constructed as one. Insulation is placed against the slab edge as well as a “wing” of insulation that extends out, away from the thickened edge, to prevent frost from driving under the slab during the winter months.
How much insulation is required at the slab edge and on the horizontal or wing, and the minimum footing depth is determined by the air-freezing index for your location. The map is backed up in the code with tables showing the air-freezing index for the individual counties in each state. The air-freezing index is defined as cumulative degree days below 32°F. It is used as a measure of the combined magnitude and duration of air temperatures below freezing. The index was computed over a 12-month period (July-June) for each of the 3044 stations used in the analysis. It is based on a 100-year average.
A frost-protected shallow foundation system is typically a monolithic concrete pour, sometimes called a turned-down slab, where the footing and slab are constructed as one. Insulation is placed against the slab edge as well as a “wing” of insulation that extends out, away from the thickened edge, to prevent frost from driving under the slab during the winter months.
The air-freezing index is like a climate zone map, (climate zones 1 through 8, with 1 being the warmest and 8 being the coldest), but instead of using 65°F as the starting temperature for the calculation, the freezing-air index uses 32°F. The scale starts at 1500 or less and has a high of 4500. Northern Minnesota has an air-freezing index of 3500; northwestern Minnesota and northeastern North Dakota have an air-freezing index of 4000. A warmer area like Georgia, for example, has all counties listed at 1500 or less.
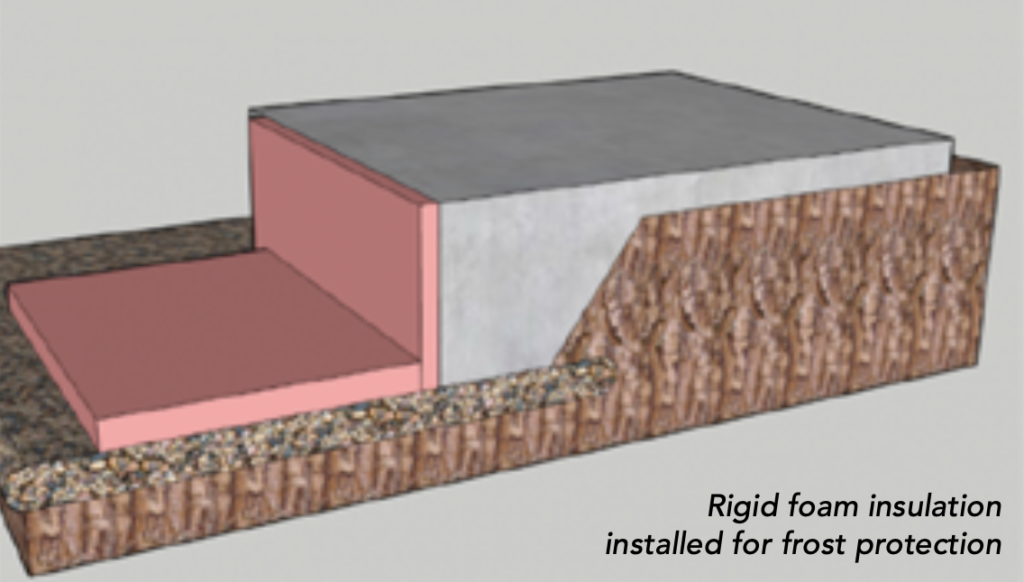
Footing depth and insulation levels
As stated earlier, the air-freezing index dictates footing depths and insulation levels for FPSFs. (See Table R403.3(1) in the IRC.) Minimum footing depths, or the portion of the footing below grade, will be between 12 in. and 16 in. depend- ing on the air-freezing index of the area. My area requires 16 in. minimum footing depth. Any above-grade portion of the footing will increase the footing’s overall thickness. So, for instance, an exposed slab edge that is 6 in. above grade will have an overall footing thickness of 22 in. (6 in. of exposed slab edge + 16 in. minimum buried footing depth = 22 in. overall footing thickness.)
At the slab edge, the insulation needs to extend from the top of the finished concrete slab to the bottom of the footing. Again, depending on the freezing-air index, the minimum R-value of insulation needed will vary. My area requires a minimum of R-9. Here’s the kicker: All insulations used below grade in an FPSF are derated. In other words, you are not allowed to use the listed R-value of the product. This is because buried insulation will absorb some moisture, and damp or wet insulation will not have the same resistance to heat flow as dry insulation. For this reason, more of the same product is needed to achieve the required minimum R-value. The reduction in R-value depends on both the type of insulation (XPS or EPS are the only two allowed for prescriptive FPSF systems) and the insulation’s density. Types IV, V, VI, VII, and X extruded polystyrene (XPS) has derated value of R-4.5 per in. for vertical installation and R-4 per in. for horizontal installation. EPS R-values are even lower, depending on the density. (See the fine print below table R403.3(1) for all the derated values.)
Referencing the above illustration and using my climate area as an example, the insulation at the corners will need to extend away from the slab edge a minimum of 30 in. (B) for a distance of 60 in. (C) from the foundation corner. The R-value of the corner insulation is a minimum of R-11.2. If the insulation is any of the XPS densities listed, the horizontal derating is R-4 per in., so we would end up using 3 in. (R-12) on the corners. The horizontal insulation along the wall is listed at R-8 and needs to extend away from the slab edge for a minimum of 24 in. (A).
Typically, I see XPS used as both the horizontal and vertical insulation. The insulation is not cut for the wing, rather it is used in its full 4-ft. width. I’ve yet to see a higher R-value insulation used in corners, as is required by code. It’s always 2 in. or R-10 (R-8 after derating).
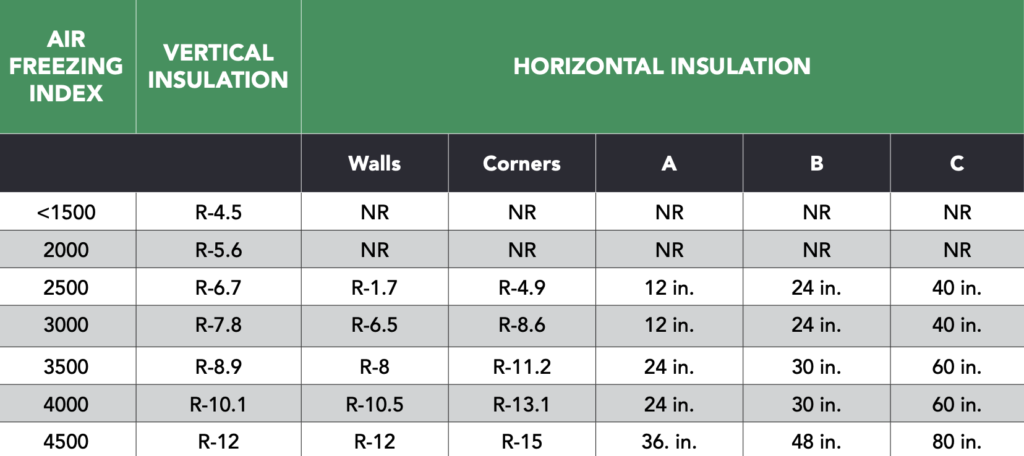
The distance away from the footing edge and R-value requirements will differ depending on if the insulation is at a corner or along a wall.
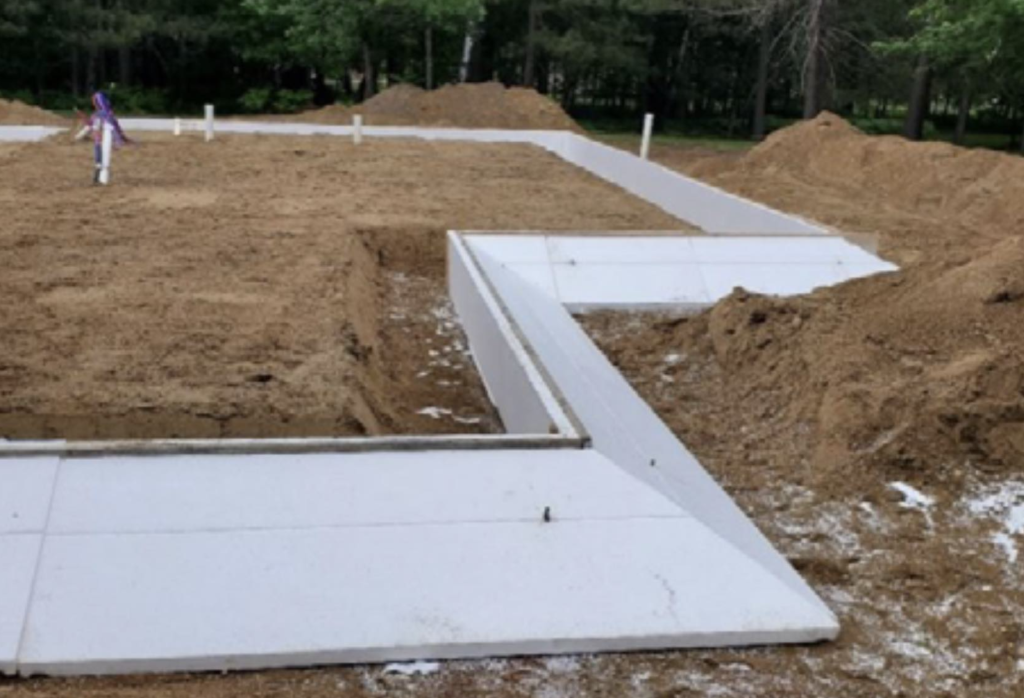
Manufactured systems
There are a couple of manufactured FPSFs. I have used the Mono Slab EZ Form system, which consists of inner and outer wedge-shaped forms made from EPS foam. The form is staked in place and a reinforcing 2x form board fits into a pre-cast slot built into the form. The outer form becomes both the slab edge and horizontal frost wing. The inner form becomes the back or inside portion of the thickened edge of the slab. The inner form is optional, we chose not to use it in the project pictured here. There are a few different versions of the Mono Slab EZ Form: a standard form, which measures 16 in. by 16 in. and is used for moderate temperature locations. Another is the Arctic Form, which measures 18 in. by 30 in. and is good for cold-climate builds. There is also a commercial form that measures 24 in. by 24 in.
Another company, WarmFörm (lead image), has a design with its roots based in Europe, though the forms are manufactured in the U.S. Another EPS-insulated form, this product looks more like an insulated raft slab than an FPSF. (Read more about the WarmFörm system here: Prefabricated Foam Forms for Slab Foundations.)
Other considerations
There are a few challenges with FPSF systems. Heating and cooling systems can be more complicated. My market commonly uses hydronic in-floor heat in FPSF homes. These systems are popular but can be problematic during the spring and fall when overnight temperatures are cool enough to warrant heating, but daytime temperatures are warm. Slab heat tends to be slow to react to temperature changes; overheating of living spaces is typical during these times of year. (For slab-on-grade projects, I prefer using a combination of hydronic slab heat and air-source heat-pump minisplit systems. Summertime cooling and spring/fall heating is supplied by the heat pump system with wintertime heating supplied by electric or gas boilers feeding the radiant in-floor tubing.)
There are also some limitations to floor coverings. Nail-down wood floorings are not an option. I see more glue-down engineered wood products being used and, of course, tile, vinyl, and carpet are common choices. Be aware that using a carpet over a heated floor will require a special carpet pad.
And finally, with FPSFs there’s no place to shelter during severe weather. I have been in a few
homes where the homeowner had a concrete shelter constructed either inside the home or in an attached garage as protection during severe weather.
Although there are a few challenges with the system, the frost-protected shallow foundation has been my go-to slab-on-grade foundation system for the past decade. I have yet to see one—when built correctly—that has failed. The worst I’ve seen is an occasional concrete crack. The biggest benefit of FPSFs is the reduced cost over other foundation systems. Affordability in new construction over the past couple of years has been an issue, so cost-savings with a reliable end-product can make this system a good choice.
One last note: For anyone interested in potentially installing one of these systems, I recommend reading the Revised Builder’s Guide to Frost Protected Shallow Foundations published by NAHB Research Center (now Home Innovation Research Labs) and the U.S. Department of Housing and Urban Development.
This article was originally published in Green Building Advisor and is shared with permission.