Feb 28, 2023
Notes From The Field: On-the-Fly Changes
Though copies of the architectural and mechanical drawings are made available before I go out to the site, surprises in the field are common. Unfortunately, the on-the-fly changes I see are often costly.
By: Karin Haerter
Codes are rapidly catching up to voluntary energy efficiency programs. So, one expects that current designers and builders are making efforts to understand and execute the necessary detailing and testing involved. As an independent HERS Rater and BPI Certified Home Performance Professional unaffiliated with any contractor or supplier, I often get calls for third party verification and testing to meet the requirements of a green program or a newly instituted code requirement. Unfortunately, my clients mostly call after the build has begun, or even when the building is nearly, or all, finished. Though copies of the architectural and mechanical drawings are made available before I go out to the site, surprises in the field are common.
Surprise, Surprise
An example is a 7-story multifamily, 13-unit condominium building which I was told was built to Passive House standards. Passive House famously requires highly insulated and very airtight energy efficient enclosures, with mechanically supplied filtered and conditioned outside air for comfort and air quality. In this case, each apartment has its own heating and cooling air handler unit concealed in a dropped ceiling, typically in a central hall area near the bedrooms. When I arrived, the first clue that the apartment duct airtightness testing was not going to happen as planned was that the location of the ceiling return access panel did not match the plans.
When I climbed the ladder and removed the ceiling panel, I saw that the location of the actual ceiling-concealed unit (duct-ed supply side only) had also been changed—for the worse.
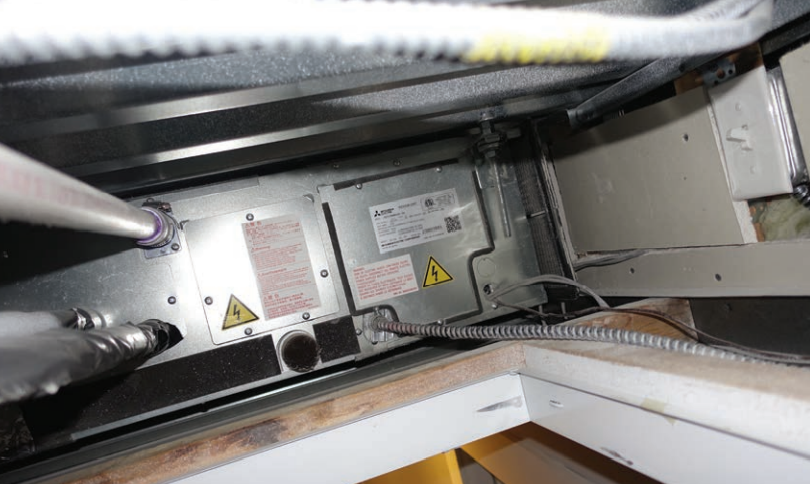
In fact, the 40-inch long opening of the return side was no longer facing the ceiling access opening as planned. Instead, it faced a framed wall with only a few inches to maneuver between the unit and the wall. Not only is the filter very difficult to remove (or reinstall), but it has to flex around utility line obstructions. Testing the airtightness of the system was out of the question: the return on the air handler could not be isolated, since the 40-inch length was impossible to properly seal.
There was also no accessing the supply side without someone cutting a hole in the finished ceiling. Protocol for the New York State Energy Research & Development (NYSERDA) Multifamily Incentive program that the client had applied for required testing the duct systems in at least 8 apartments. But, most of the apartments had the same access problem.
Unfortunately, on-the-fly decisions are not rare, even after a project has involved months or years of planning before ground is broken. In a case about 2 years later, I encountered exactly the same on-the-fly relocation of a ceiling concealed unit at a newly completed and occupied certified Passive House 5-unit condominium. It had already passed the whole house air leakage requirement for Passive House. After completion, the condo board opted to qualify the property for the same NYSERDA incentive program mentioned previously, thus the retroactive need for individual apartment blower door and duct test results.
The apartment tests went decently, but the location of the concealed ceiling air handler units prevented testing. When the client pulled out the onsite plans, sure enough, in red ink, someone had drawn in the change in the location and orientation of the air handlers. The client admitted that the HVAC contractor had suggested the change, and a project architect approved it, though no one could recall the reasoning for the change.
Afterthought not Forethought
How do on-the-fly changes happen? In the more recent case, it clearly was the result of the HVAC contractor on the job talking the responsible party into making the change without consulting the rest of the team to find out why the plan was drawn the way it was. (Was it to save money? To save time? Because it “makes sense”?).
In the earlier incident, multiple changes in the project management team during the build caused lapses in continuity. The HVAC team was also replaced at some point. The foundation and first floor were apparently completed before the client decided to build to Passive House standards. Even later, after the building was nearly complete, the client wanted to apply for the state incentive rebates. That’s a lot of changes on-the-fly!
A typical scenario might go like this. A project manager in the office actually reviews the plans and says, sure we can meet the energy code (or program under consideration), no problem. Perhaps the manager then passes the responsibility to a field superintendent, who in turn informs any team workers and subs that energy detailing would be part of the job. But after the initial meetings, how much actual time is spent to make sure the site workers understand or receive actual illustrated instructions or training on how to do this detailing? Likely no one gets assigned the responsibility for checking the details.
On-the-Fly, Not-so-Good
On-the-fly changes are costly. In the case of the examples above, both clients had to give up incentive bonuses offered through a state program, because the duct airtightness verification is a requirement to qualify. (And, had to pay me for my trouble.)

More unsettling is the subsequent decision of the 13-unit condo’s manager. He had all the filters removed from the air handlers, and instead installed off the shelf filters just above the ceiling return access panel. So, the return air from the apartment is now filtered through the access panel, but the ceiling plenum air is not, allowing dust and fiberglass, at the very least, into the apartment’s air supply to the occupants, potentially compromising their health. In addition, the air handler’s exposure to unfiltered air could compromise the efficiency of the unit, reduce its useful life, and void the unit’s warranty. Talk about cost!
On-the-fly changes can occur in any part of a project. However, in the wider world where many contractors have no previous experience with energy efficiency details, and especially where codes have not yet caught up, these details in particular are often not even on contractors’ radar. Misunderstandings by those not familiar with energy efficiency requirements are endless.
Whether things go right or wrong starts with the plan designs and written contracts with subs. Plans rarely have energy efficiency details written out and clearly illustrated. Instead, a reference is made to, for example, “work must meet requirements of NYEEC 2012.” Contracts with subs are written in general terms, referring them to the plans. Having a construction team member assigned to track the details necessary to meet programs or energy codes is rare. Even if there is, that person is likely to have numerous other time-consuming responsibilities that distract from energy efficiency oversight.
Frequently, when changes are made during the build, not everyone on the team is informed. In many cases, the energy detailing seems to be an afterthought, instead of part of the process. Compounding this lack of clear communication, in places where low ball pricing often gets the job (and that is part of the problem), there is little incentive for contractors to spend money to train their teams. Plus, there is usually intense pressure to get the job done on tight deadlines.
One 40-unit project did include a section of the plans explaining the energy efficiency requirements, including actual copies of required Energy Star Checklists: HVAC Design Report, Water Management Checklist, Rater Field Checklist, and HVAC Commissioning Checklist. But believe it or not, I was told by key personnel that they had not seen them, did not know where to get copies, or were not given copies. This from subs who also had full copies of the plans.
Some Good News
On the positive side, one of the best success stories was at an 11-story multifamily building, where exhaust ducts tested substantially better than their targets. This was not by chance; the architect had specified explicitly, and with drawings, how the ductwork was to be installed. The architect included a clause in the contract that said the resulting work must pass an airtightness check. With that in the sub’s contract, the HVAC contractor knew that the responsibility for delivering those details was his, and he was present for the resulting successful testing.
Of course, widespread education of the general public is a high priority. But many consumers are already impressed with concepts like “built to Passive House standards,” “low carbon footprint”, and “healthy living”, and the market for such homes is growing. According to some studies, such as by the National Association of Home Builders (NAHB) and academic researchers, people are willing to pay higher rents and purchase prices for energy efficient homes.
But the progress of energy efficiency in construction is still hampered by building professionals lacking in understanding of the detailing and oversight that make energy efficiency work. Getting the professionals in the building industry, contractors, and trades up to speed appears to be a bigger job than convincing consumers of the value of an energy efficient home.
Passive House is a voluntary building standard that achieves very high energy efficiency through the use of maximum insulation, combined with very airtight buildings, carefully designed heating and cooling strategies, and dedicated exhaust and ventilation mechanicals. To qualify, a home needs to pass an airtightness test (0.6 ACH50) and prove through modeling that it uses minimal energy. I pointed out the Passive House participation of both projects above, since it is an ambitious and laudable goal.
But, if you’re going to go all in on a project, it would make sense to pay attention to details. The on-the-fly changes actually make the air handler units more difficult to maintain, which affects both the energy efficiency and the air quality. So, in this case, changes on-the-fly undermined a good thing.