Apr 7, 2021
Four Domains of a Resilient Organization
John Tooley shares 4 top tips for making and maintaining a resilient organization.
By: John Tooley
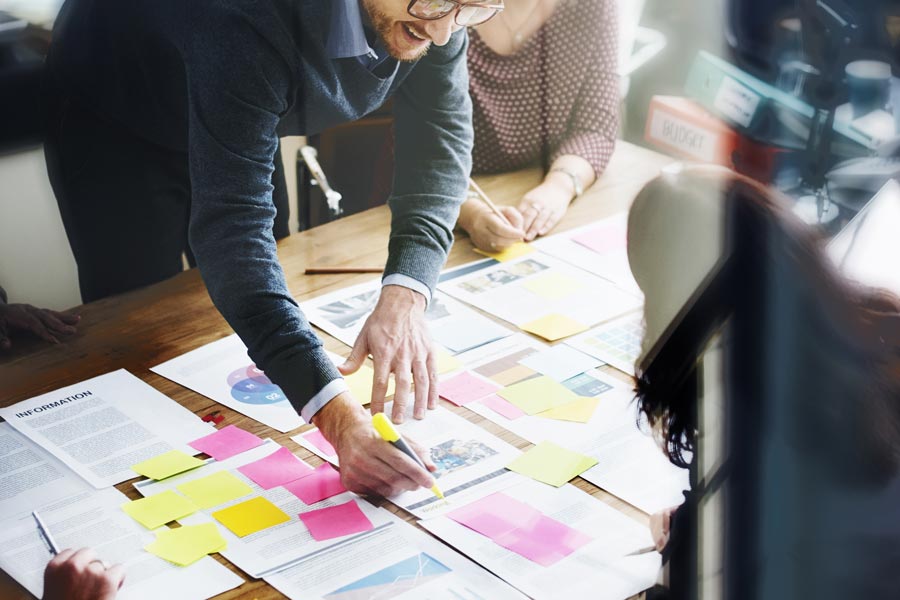
Our greatest weakness lies in giving up. The most certain way to succeed is always to try just one more time.
Thomas Edison
COVID has resulted in a new normal and will demand resilience. These times of reduces cash flow and revenue, managing change, retaining good employees, and adjusting to fear, stress, and anxiety are that new normal.
As stated in Psychology Today, resilience is the psychological quality that allows some people to be knocked down by the adversities of life and come back at least as strong as before. Rather than letting difficulties, traumatic events, or failure overcome them and drain their resolve, highly resilient people find a way to change course, emotionally heal, and continue moving toward their goals.
There are four areas every organization must consider as essential needs:
- Defining the purpose for our work,
- A strong culture,
- A strategy and tactics to support our purpose, and
- Standardizing our work and processes.
Let’s look at all four of those in more detail.
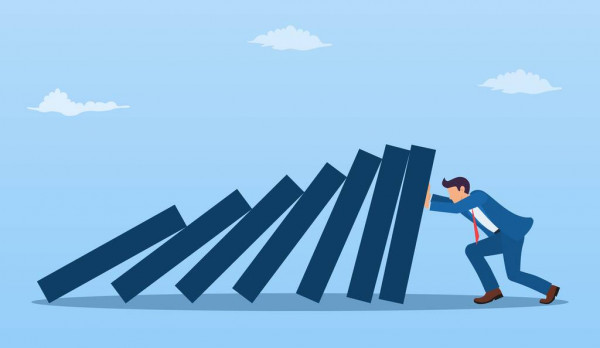
Purpose
Defining our purpose is central to what motivates our workplace. We need to find meaning work that offers purpose, fulfillment, contribution, connection, and hope. It is a necessity to define what our company is dedicated to and for what purpose. It is important to positively express it and how it will impact others. Helping others is our greatest prize in life.
Culture
Culture trumps a well-planned strategy and tactics that guide the whole organization when delivering our products or services. A good culture is one that is safe. One that is blame free, one where management trusts employees, where pride of work is high, and where teams have an extraordinary level of comradery. A good strategy and tactics without a good fertile culture increase hassle, expense, and human effort.
Strategy and Tactics to Support Our Purpose
If one assumes that employees that do work wrong with intention have let go, that leaves us with those who want to do their job right. If there are deficiencies with this group, it is not an act of intention and can be the result of low morale or lack of knowledge, skills, and/or abilities.
Each of these is the responsibility of management and leadership. They are responsible to help employees obtain their fullest potential. Therefore, each must take full ownership of unintentional deficiencies and inefficiencies. An exception might be that some people do not, nor will they ever be able to perform our work. It is unfortunate and by no fault of their own, but we cannot keep them and must let them go.
Standardizing Processes
When there is (1) stress, (2) hassle, and (3) misunderstanding, it often means there is something that has not been standardized, agreed upon and then codified. These three things cause excessive expense and unnecessary work effort. Standardizing our organization’s plumb lines to guide our work is very important. There is little opportunity for overall improvement without a plumb line to compare present actions. Comparing our work against our agreed upon specifications helps reduce personal opinions about the quality of our behavior and work.
Agreed upon specifications or requirements are developed by a program or management. New and existing employees agree to follow all standards set forth by either.
The Lean Enterprise Institute defines standardized work as one of the most powerful but least used lean tools. By documenting the current best practice, standardized work forms the baseline for continuous improvement. As the standard is improved, the new standard becomes the baseline for further improvements, and so on. Improving standardized work is a never-ending process.
All work is a process; therefore, standardization must be an ongoing work across the entire organization. This work effort is no place for the Lone Ranger. It is the product of the entire management and leadership. They may commission someone in the organization to develop a standard, but it must be agreed upon by the entire leadership team and then trained and implemented. Standardization is not static.
We have discussed the following areas we can improve.
- Our need for a well-defined purpose,
- A superior culture,
- Management and leadership accepting complete ownership for deficiencies, and
- Standardizing everything we do.
Once we have a strategy that includes agreed upon specifications, we are ready to align and standardize training and inspections.
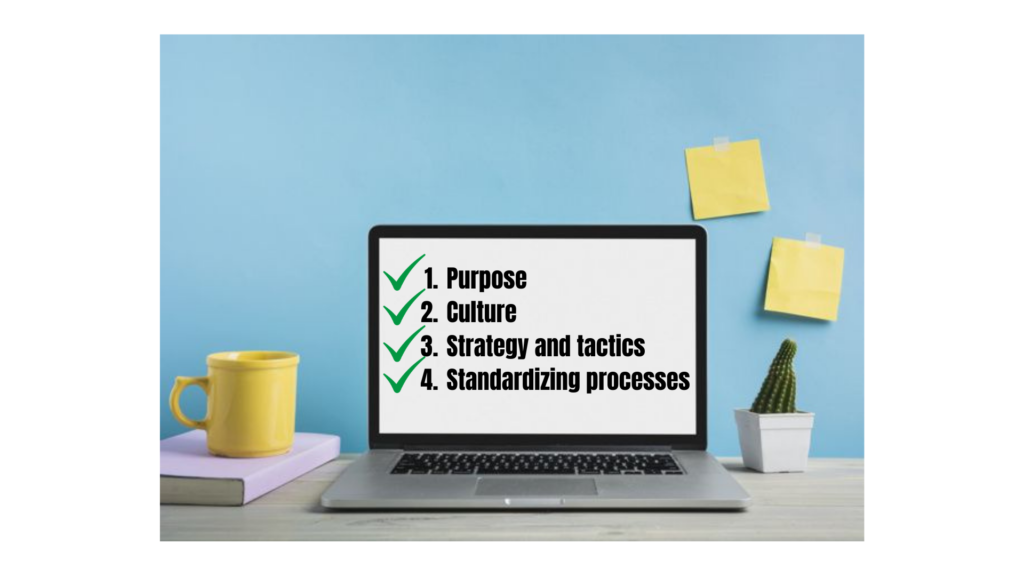
Training
One of the most important company transformations is educating everyone about our culture and why we do what we do. We know we must also teach them how to do the work we do, and how to do it right. These important areas cannot be accomplished without standardized training, specific, and structured communication processes.
Standardized training results in standardized work. Each task must have a training process that clearly lays out the task in logical steps. Documenting logical steps that move the work forward, each step should have key points that point out what will make the job easier, make or break the job or could cause an injury. It is best to have and document clear reasons for the key points. This approach is taught in a very structured process. Each employee should have a training log to document when a task is mastered. The training log and an employee’s progression can be linked to a career ladder.
All work tasks must be trained to a level of competency to complete all tasks defect free and in compliance with agreed upon specifications. It is also important to include the organization’s best practices. They too must align to the agreed specifications. Anything less than this will result in failed quality assurance inspections, increased expenses, and customers not receiving their desired outcome.
Inspection
During my experience and studies, I have found that there are three types of inspections: judgment, informative, and source. The latter two allow feedback and help project managers, crew leaders, and contractors, focus on improvement of the work process and on prevention of mistakes from becoming defects. These two inspections must not result in fear in the workplace.
Judgment
This inspection type is exactly as stated, judgment. It often is accompanied with fear. The main objective of judgment inspection is to detect and correct defects thereby stopping them from reaching the customer. The focus of the inspection is products, and services and how they match up to specifications, codes, scopes, manufacture specification and standards. This form of inspection is done after the work is completed and it is too late and costly to fix. The degree of product excellence is equal to the level of inspector knowledge, experience, and attention. This form of inspection should be replaced with informative and source inspections. An example of this kind of inspection is code inspections. We cannot inspect quality into our products and services. We must build quality into the process of work.
Informative
Informative inspection is an inspection in which, when a defect occurs, information is fed back to the person and work process involved, which then takes action to correct the process. This approach is centered on all work is a process and all defects are caused. If defects are caused, then they can be prevented. Informative inspections are focused on prevention. The objective is to prevent errors in the process and therefore eliminate defects in the retrofit of buildings. Immediate feedback for improvement is primary. We can divide informative inspections into two categories.
- Successive inspection by the trade that is about to begin work, frequency is 100%. Successive inspections are conducted by the trade that is about to commence work. They inspect critical details that will be covered up by their work, will cause their work to be defective or cause errors unrelated to the work they are about to do. An example might be where the attic prep is finished and passes the attic on to the insulator. The insulating person first inspects the air sealing and prep per the critical details and specifications. If no defect exists, he or she carries out their work. Successive inspections are an objective inspection on 100% of the houses. For an insulator to be skilled on a critical detail and specification inspection there must be a simplified process and training that clearly identifies each detail done properly.
- Self-inspection also known as mistake proofing verification conducted at the time work is completed on 100% of tasks. Self-inspection is just as stated. The installer inspects his or her work against trained specifications to assure no mistake has occurred. Defects found are immediately corrected to assure a mistake does not become a defect. Immediate feedback allows the installer to continually improve and become more efficient. This inspection type is the least expensive and is a step built into the work process.
Source
Source inspection determines “before the fact” whether the conditions necessary for high quality production exist. “It had dawned on me that the occurrence of a defect was the result of some condition or action and that it would be possible to eliminate defects entirely by pursuing the cause” [Shingo, 1986, p.50]. Examples of source inspection are backing knee walls to eliminate thermal anomalies and a sealed combustion appliance requirement if installed inside the conditioned space. Requiring either of these “before the fact” will result in the elimination of defects associated with either.
A Strong Foundation
Which came first a good culture or standardized work? Standardized work will never reach our desired result without a good culture. A good culture is hard to maintain where standardized work is not established. The lack of either results in putting out the same fires over and over. “Culture eats strategy for breakfast,” a phrase originated by Peter Drucker and made famous by Mark Fields, President at Ford, is an absolute reality!
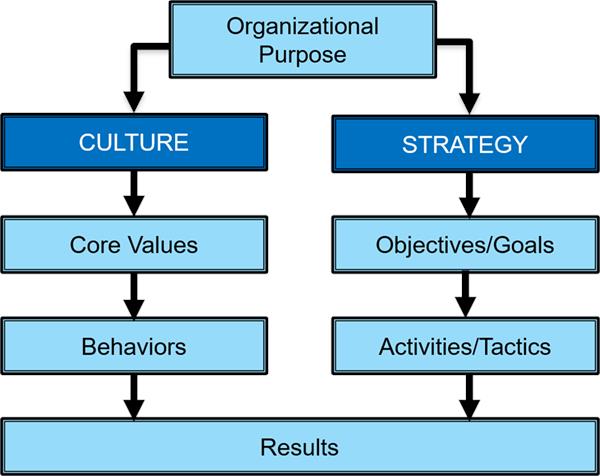
Purpose, culture, strategy, and competency of task supported by competency training are like the four legs of a table. Together they deliver a strong foundation for a great company to work from. The most important leg being culture. The reason most cannot compete with Toyota is they can copy their strategy but cannot copy their culture. The remaining three legs are the way we maintain our organization’s purpose. The challenge is complementary alignment and development of each. Each leg is essential, but none alone is sufficient to develop a superior sustainable organization. They are interwoven by their interaction. They should be developed in a fertile soil of respect for people, continual improvement, and a culture of prevention. I have learned small improvements build into large transformational change. Be patient and know your dedication, persistence, and effort will bring the desired results you want, a strong sustainable organization.
Do not judge me by my success, judge me by how many times I fell down and got back up again.
Nelson Mandela