May 13, 2021
Retrofitting Manufactured Homes—Part 2
Learn about Slipstream's production-based duct-sealing/distribution repair programs.
By: Bob Pfeiffer
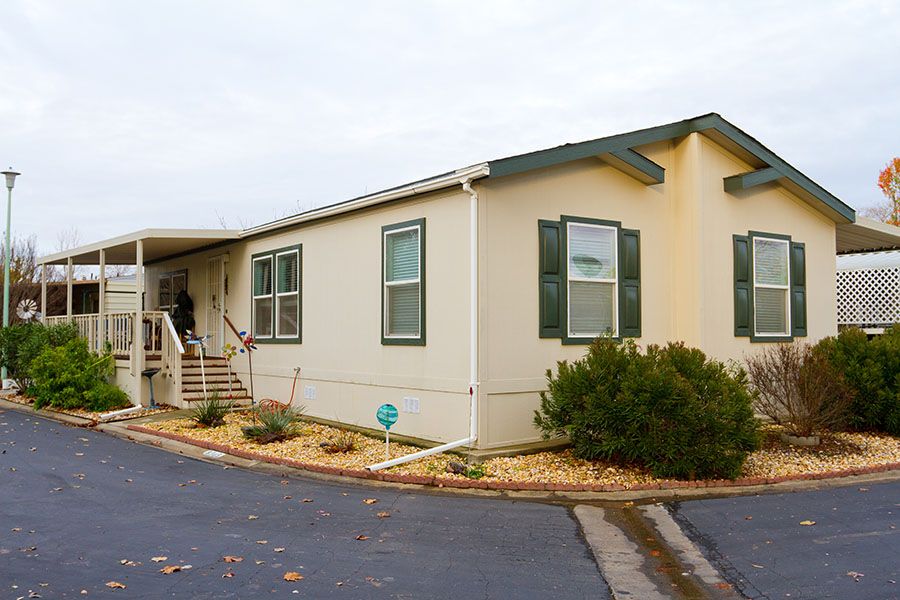
This is part two of Retrofitting Manufactured Homes. You can read part 1 here.
The duct-sealing/distribution repair programs Slipstream delivers are production-based. That means we don’t need exhaustive, time-consuming testing. Our preferred method is to take pressure pan readings at each register @-50 Pascals. This approach is quick, easy to teach, and gives us enough information to assess duct condition and relative location of leaks.
- Air handler and exhaust appliances are turned off. All registers are open and cleared of surface obstructions.
- House is depressurized to -50 Pascals using a blower door.
- While at -50 Pascals a pressure pan, attached to a manometer reading pressure differential, is tightly positioned over each register, one at a time. The results are recorded on a worksheet. (See image below.)
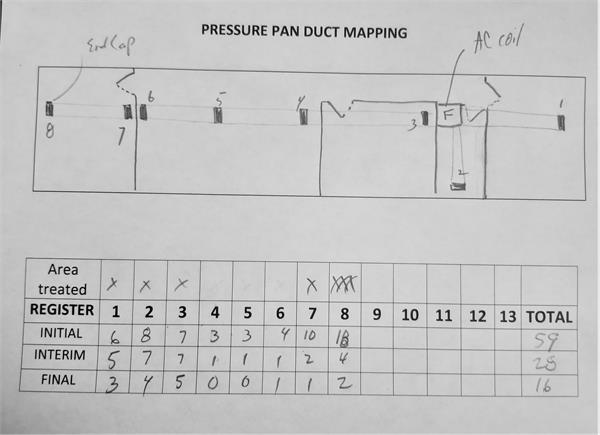
- Add readings to obtain gross leakage number.
- Large numbers equal large leaks; large leaks can be found closest to the large numbers.
At what point do we stop sealing? Or even begin to seal?
Ductwork isn’t like an inner tube, where the correct answer is “when you’ve plugged every leak.” Budget, accessibility, time, and myriad variables all contribute to a logical endpoint. Let’s look at some of the existing conditions we face and consider some strategies.
Condition
I have been a trainer, installer, and technical advisor to many Duct-Sealing programs across the Midwest and have crawled under hundreds of units. Most are in disrepair, if not in complete shambles. These blow-outs may have been created by or create pathways for animals and cold air to enter and create chaos with any work we attempt.
It is imperative to eliminate the ability for cats, raccoons, etc. to gain entry to the crawlspace. The skirting must be intact!
Location
Past logic stated that the further north you are, the more you must be concerned about freezing water lines, unless you are performing a complete floor cavity, water line insulation, and road barrier retrofit. The February 2021 Texas freeze-out changes all that. We simply MUST expand the parameters of weather eventualities as we design and work on these units, especially their vulnerable component-exposed plumbing. Duct-Seal-Only or Seal with Minor Repair programs must change to make some provisions for this:
- Install pipe wrap on all accessible water lines.
- Insulate the rim and under-pipes that run to exterior walls.
- Patch all gross holes in the road barrier. (See photo; this pathway into the attic cavity is a major leak in the distribution system.)
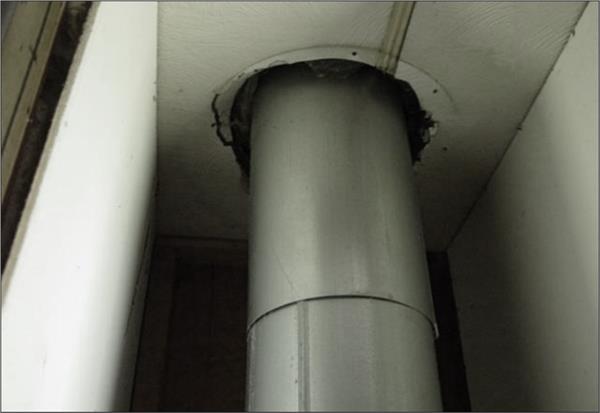
- Assure skirting is intact and will remain so during winter months.
- Seal only large holes, leaving a small amount of conditioned air to warm the air space. Remember, it is cheaper to keep the pipes open than it is to hire a plumber and send a crew to repair the road barrier and damaged relations with your client.
Age and Condition
Newer units will have up to R11 under the ductwork, such that heated air leaking into the belly is not completely lost in winter. This is more of a serious concern in climates requiring a lot of cooling. The road barrier is usually intact. Registers are located on the perimeter. Most leaks will be at take-offs, requiring access through the road barrier.
You notice I am offering no absolute leakage targets; over the course of my career, I recognize it as a recipe for chaos. The very best I can offer is to know your conditions and variables both physical and behavioral; after all, we are serving people. That said, a simple guide to be applied to the entire system:
- Assure sufficient airflow,
- Seal big leaks,
- Easy, accessible leaks next,
- As you proceed, factor-in unintended consequences, comfort, program costs, and
- Assure all work is durable.
Program design demands metrics, a means to quantify savings and benefits within a cost-effective framework. Those are projections, based on reasonable assumptions, but nothing is better than going back to houses you have worked-on, performing post evaluations to determine how installed measures perform over time, what does and does not work for you in your location. The information I have presented here works for us in the Midwest; but in an ever-changing environment we must be vigilant to stay ahead of the curve and use our abilities and gained knowledge to offer the very best services to our clients.