Jul 21, 2023
Should a Builder Own a Blower Door?
Yes, according to this high-performance builder, who uses it to constantly raise the quality bar.
By: Ben Walker
With codes and high-performance construction programs requiring airtightness testing, a small but growing cadre of home builders have been purchasing their own blower doors. They are finding that this tool’s value goes beyond mere compliance.
One of them is Arrow Building in Columbia, Missouri, which owner Jake Bruton says builds “durable, energy-efficient, aesthetically pleasing homes.” Most of his projects meet Passive House standards, which specify a maximum air leakage of 0.6 Air Changes Per Hour at a test pressure of 50 Pascals (0.6 ACH 50).
He bought his first unit in 2014 before committing to those standards. He heard murmurs that air tightness testing would eventually be part of the code. No other builders in his market seemed to own one, so he figured that being the first would give him a competitive advantage.
Bruton builds custom homes, but some Zero Energy production builders also own blower doors. One is Thrive Homebuilders in Denver, which completes about 100 homes per year. Company president Gene Myers says it’s an excellent tool for quality control. “It’s particularly handy for townhomes, where party walls can be a challenge with airtightness.”
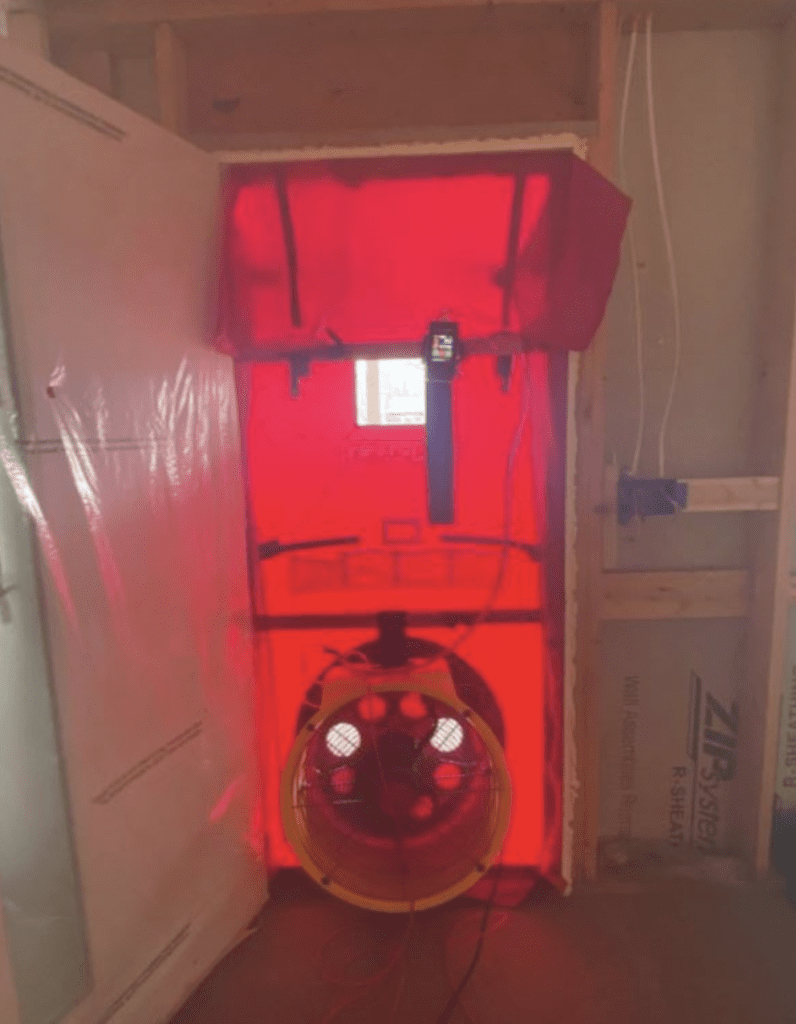
Driving Improvement
Bruton says the blower door proved its worth immediately. “We started testing everything to educate ourselves,” he recalls. Although his new homes were coming in at a code-compliant 3ACH 50, he wanted to do better.
So he began looking online for best practices in air barrier detailing. “We found architects that had done multiple Passive Houses and started calling and asking how they did it,” he says. Test results quickly fell to 1 ACH 50 or better.
To maintain those numbers, he now performs three separate tests on every new home, as follows:
Test # 1: Sheathing. The first test is for overall envelope tightness. Arrow’s homes are designed with a hybrid air barrier that includes the exterior sheathing and the ceiling below the attic. Both are installed and taped before this first test.
The framers don’t cut out window openings yet: instead, they only cut out the door opening where the blower door will be installed. And rather than the standard 50 Pascal test procedure, they depressurize the house to 100 Pascals, then spray the outside with a hose to see if any water gets sucked in through unsealed seams and holes.
Bruton sometimes gets asked about pushback from the drywall contractor, who has to come to the house twice. His answer is that Arrow’s homes are trussed to eliminate the need for interior load-bearing partitions. “The ability to install the lid in one monolithic run before we build those partitions saves the drywaller time in the long run,” he says.
Test # 2: Windows and Doors. With the first test complete, crews install all windows and doors, after which Bruton runs a second test. Since the envelope has already been verified tight, this test pinpoints any problems with the window and door installation.
Bruton will also sometimes do another test, which is basically #2A. It’s done before the drywall goes up, for instance after the spray foam insulation has been installed or after the mechanicals are roughed in. It depends on the home and the complexity of the details.
Test # 3: Everything Else. The final test is performed post-drywall at the standard 50 Pascal pressure, during which a fog machine is used to identify specific leaks that might have been added after the windows and doors have been installed, usually from electrical and mechanical penetrations.
The local jurisdiction also requires third-party testing, so this final in-house test ensures a passing grade.
Setting up and running a test only takes an hour, but Bruton shuts down production for each of the three days so there’s enough time to fix any problems. “It’s a worthwhile investment to ensure quality,” he says. “Besides, weather delays eat more time on a build than the blower door tests.”
The Retrotec Model 5000 blower door Arrow uses costs about $3500 and has proven a great investment. “The tests we do guarantee a much better home for our customers, and we couldn’t afford to do them if we didn’t have our own blower door,” he says.
The unit works with Retrotec’s GaugeRemote app, which lets the operator control fan speed from a phone or tablet, as well as its rCloud app, which geo-locates the home, adjusts for local weather conditions, runs the test and generates a report that can be saved, shared or printed. These apps mean the operator no longer has to take notes and can control the fan remotely while moving around the house focusing on finding those leaks.
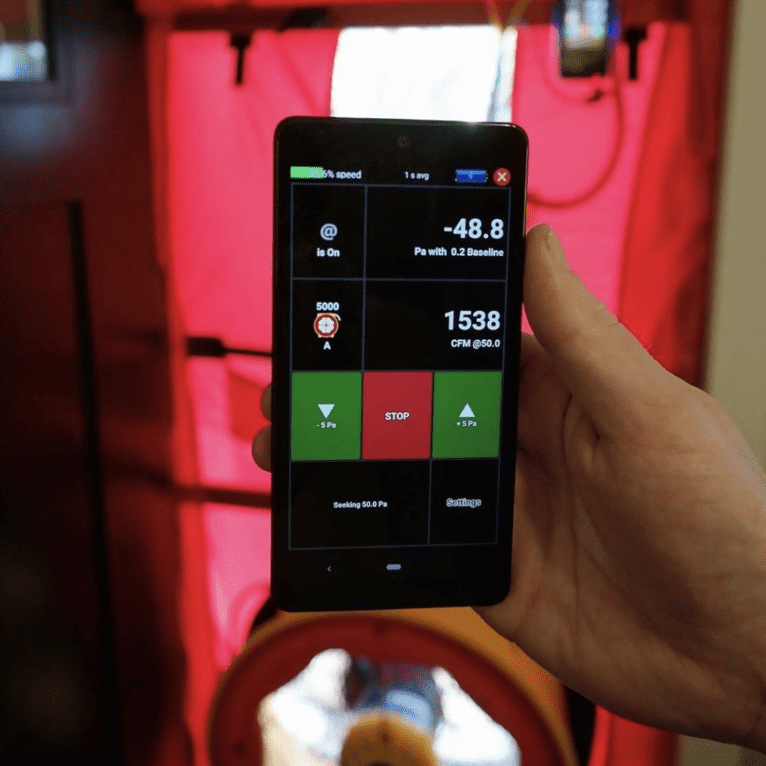
Trust But Verify
Bruton stresses that his company’s path to better air sealing didn’t require radical changes. “We did switch from using house wrap as the exterior air barrier to using the sheathing, but otherwise don’t detail our homes much differently than before,” he says. “We mostly just pay more attention to the critical details. If the plans call for a bead of sealant, we make sure that whoever is responsible for that part of the job understands how to install that bead correctly.”
The blower door also lets Bruton confirm that subs are meeting Arrow’s air sealing specs. For example, spray foam installers’ work can be tested immediately, not weeks later. In addition, no one is allowed to drill holes without getting them approved, and everyone is responsible for sealing their own work. Subs are given cans of spray paint, with each getting their own color, and are required to mark all their penetrations. If they drill a hole without approval and the test shows that it leaks, they have to pay to fix it.
That’s seldom a problem. “Although we verify everything, we work with conscientious, high-quality subs,” he says.
The bottom line is that the ability to test when needed has made it possible for Arrow to refine its construction systems and raise the quality bar for everyone on the job. “The blower door is one of the most important tools we own,” says Bruton. “I don’t think we would be as good today without it.”
For more information on Jake Bruton’s work, check out his articles at JLConline.com, or his videos at BuildShowNetwork.com.
This article was originally published in the Retrotec blog and is republished with permission.