Nov 26, 2024
Field Quality Control and Rebate Programs
In the end, the message is clear: We need to work with contractors and help them do better work.
By: Charley Cormany
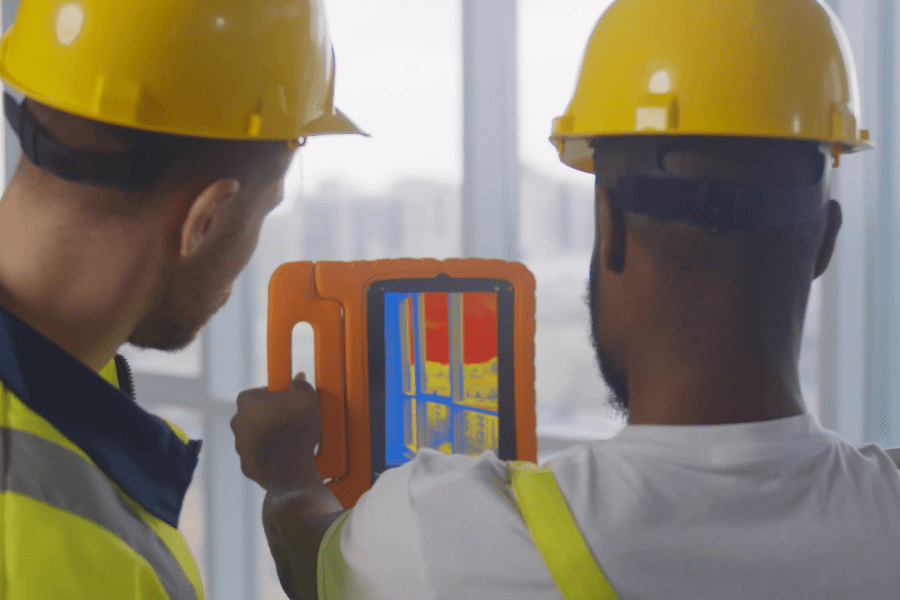
Efficiency First California’s primary mission is to help contractors succeed in transitioning to a clean energy future. Converting buildings from fossil fuels to electricity generated from renewable sources is a critical step in this process. As part of our mission, we also strive to support the industry’s growth as a whole.
One way we support the organization is by providing utility support services. Our work as program implementers, managing utility rebate programs, helps support contractors. We share our successes with other rebate programs in the state with the goal of making the rebate process easier for all parties.
Through this work, we’ve learned that consistently achieving high-quality installations requires robust quality control and active partnerships with contractors. We are now using targeted mentoring to improve quality. Mentoring can be expensive, but if done correctly, it can be surprisingly cost-effective.
One of our larger contracts is with the Sacramento Municipal Utility District (SMUD). In addition to desktop quality assurance (QA), we perform Field Quality Control (FQC) inspections on a percentage of completed projects to ensure they meet program requirements.
Having verifiers in the field daily, looking at jobs after they have been completed and inspected and the rebates have been paid, gives us a unique perspective. We see hundreds of jobs after the contractor is done, the HERS raters have done their thing, and the local building officials have signed off on the project. We currently have roughly 400 contractors in our residential programs, and last year, we processed over 5,000 projects.
You might assume that after all the attention to permits, inspections, and third-party verifications, most of our inspections would be routine. The reality is that even with the various safeguards in place, we find issues in the field regularly. Some of the concerns we find are honest mistakes or lack of understanding. Some are not.
In the SMUD program, contractors are required to correct issues that our verifiers find at no cost to the consumer. Trust me when I say we know how expensive it is for a contractor to complete “corrective actions” returning to a completed project to make minor adjustments. It is safe to say that most contractors would prefer to improve their process and the quality of their work so they don’t have to return to a completed project.
Unlike many rebate programs, we take a pragmatic and collaborative approach to working with contractors. Let me explain what we’ve learned about quality control and how we work with contractors to achieve better results. I want to share some of my observations about what we find in the field and dispel some common myths.
Pricing is More than Being Cheap or Expensive
The triple bid process, which has become a standard practice, often promotes being the lowest cost option over the best value. But the real value is more than being cheap or expensive. Our program has some contractors who do great work and have low overhead. They can provide great value at a low cost. We also have larger shops with multiple crews and high overhead costs. Some of the bigger shops do great work and are usually more expensive.
The majority of contractors we deal with are small mom-and-pop shops. For years, there has been a perception that larger or union shops provide higher quality results. Our program has several large companies, and a few are union contractors.
There is no question that larger and union shops charge more when we review contracts as part of our submissions. Unfortunately, we don’t see a direct correlation between union and non-union projects regarding quality. The same holds true with size. A few of our big players struggle to meet basic program requirements.
Unions provide good training and a pathway for employee growth, which is important. However, the size of the company or its union affiliation is not necessarily a good metric for choosing someone who will do quality work. What matters most is company culture—how dedicated leadership is to maintaining high standards throughout the business.
Company Culture Matters
If the business owner is focused on volume over quality, it is difficult for the workers in the field to improve their work. They are most likely not given enough time to address the details that make the difference between a good enough job and a great result. We must find a way to reward contractors based on quality of work and actual value over price alone.
With SMUD, we strive to provide high-quality and effective finished projects. This means we require many things to be above building codes. If we were using a grading system, we would aim to promote B-plus and A-level work. Work that meets the building code’s minimum requirement would be a C or C minus.
In general, contractors are consistent—they do good work, or they don’t. There is some variation, as the same company might do great work with one crew and mediocre work with another. Again, this points back to the company culture, as quality control starts at the top with the company’s owner.
One thing that might surprise you is smaller shops often provide better quality results. I suspect this is because the person at the top is closer to the day-to-day operations. Subcontractors are essential, too. The person hiring the subcontractor must convey expectations regarding attention to detail and quality. We often send contractors back to clean up things their subs have skipped or were not aware were required.
Third-Party Inspections Don’t Catch Everything
Many think all is well if a building official signs off on their project. I understand why; the goal of building inspection is consumer protection. Another third-party inspection process is the Home Energy Rating System (HERS) certification. The HERS process is designed to provide feedback on a building’s energy efficiency. You would think a project that passed HERS compliance testing and a building inspection would be in good shape. We inspect projects after passing both HERS compliance testing and building inspections. This means we see the effectiveness of both processes on completed projects. Even with these safeguards, we find issues frequently; some are serious.
There are a few things we find regularly. One of the more serious is natural gas leaks. SMUD’s residential programs concentrate on converting gas appliances to electric ones. The two biggest targets are gas furnaces and gas water heaters. Our contractors are replacing the gas units with electric heat pumps, a more efficient and much cleaner solution. Once the conversions are complete, we check the remaining gas infrastructure to ensure safety. Unfortunately, we find gas leaks all the time after the project has passed both a building inspection and HERS compliance testing.
Why? I suspect that looking for gas leaks is not one of the checkboxes on the building official’s list. That is a real shame. If it were up to me, I would require them all to carry a gas sniffer, like our verifiers. Natural gas leaks are dangerous, and methane is a potent greenhouse gas. The scale of these so-called “fugitive emissions” is enormous.
Another common problem is improperly sized fuses. Most high voltage (240v) equipment utilizes a fused service disconnect. A disconnect is a small breaker box located within the eyesight of the unit. The disconnect lets a person service the unit with absolute confidence that no electricity flows through the wires. Service disconnects must be clearly labeled with the maximum fuse size. It seems trivial, but it is a code requirement and can be dangerous if missing. If a technician or homeowner installs the wrong fuses, the wires feeding the disconnect can overheat and cause a fire; that’s a real issue.
We often see problems with condensate lines. Heat pumps, like air conditioners, remove moisture from the air during operation. The excess moisture must be properly drained or pumped to a safe location. Condensate drains are a standard part of HVAC installations. Heat pump water heaters, unlike their gas counterparts, need condensate drains. We see lots of issues with these.
A common mistake is sharing a condensate drain with a pressure relief circuit.
Another is the drain’s location. Often, these drains are not in a suitable location, for example, on a sidewalk, where the water could freeze or, more likely, cause a buildup of slippery slime that creates a fall hazard. I suspect some of this is because most building inspectors are not as familiar with the nuances of HVAC installation as they are with carpentry, plumbing, or other trades.
Poorly installed ductwork is another area both HERS raters and building officials should pay attention to. Crushed ducts, poor design, and improper sealing are common. Insulation is ripe for improvement as many contractors don’t follow proven installation methods.
I don’t fault inspectors for missing these things as much as the process. In reality, inspectors are often overloaded with work, tight on time, and just trying to do their best. I caution program managers who rely on the building officials, or HERS raters, for quality control. You need to have your own people in the field looking at projects if your goal is quality.
Helping Contractors Do Better Work With Targeted Mentoring
So, how do we help contractors do better work? We have found that the best solution is to partner with our participating contractors by offering on-the-job training (OJT) via mentoring. Mentoring looks expensive, but it can be cost-effective if targeted correctly. Let me explain.
We have spent a ton of money on training materials for our participating contractors. We provide a learning management system (LMS) with hundreds of videos and other training resources. SMUD has spent tens of thousands of dollars to make this information available to our participating contractors. That is a generous thing to do and a good step toward getting higher-quality results. The problem is that only some people take advantage of this vast information resource. You can lead a horse to water, but…..
As a result, we have shifted our approach and now use funds allocated for educational materials for mentoring. Our current process is to identify issues a contractor needs help with and let them know we see these issues regularly. We then set up a mentoring session and help their crews learn how to overcome the challenge. Our mentoring efforts concentrate on a specific issue, which allows us to use our verifier and the contractor’s time effectively.
Targeted mentoring has become a game changer for us and our contractors. When we train contractors, they submit projects that require less oversight during the desktop review, which saves time and money. The contractor’s corrective actions are reduced, which saves them time. Our verifiers can do more inspections when there are fewer issues. It turns out that targeted mentoring can actually save money if your process is dialed in.
SMUD supports us in this effort, and we both see it as an investment for our participating contractors. The contractors who have taken advantage of our free mentoring truly appreciate working together to resolve issues. Our field inspections are no longer a cause for concern but an opportunity for the contractor and the program administrator to learn. Ultimately, our role has changed from compliance to education, which is a great solution.
In the end, the message is clear. We need to work with contractors and help them do better work. Our partnership approach has been more effective than providing training materials that no one uses. Ultimately, we all want the same thing: high-quality, effective projects installed by contractors making a decent living. Contractors are on the front lines of for a smooth transition to a clean energy future.