Jun 22, 2022
Taking the Lead on Lead
Lead, as used in lead-based paint (LBP), was a staple of the coatings industry in the United States for well over 100 years. Lead, in different compounds, appeared to be the all-purpose solution to any painting problem. Adding lead to paint increased its durability, because the tiny lead molecules carried the paint into pores and other irregularities of the surface being coated.
By: Gregory Runevitch
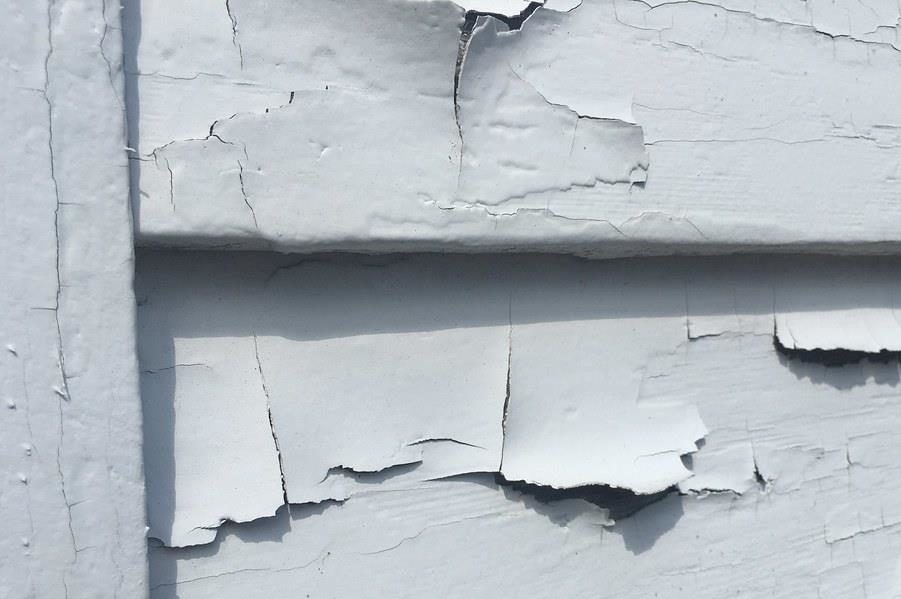
Lead, as used in lead-based paint (LBP), was a staple of the coatings industry in the United States for well over 100 years. Lead, in different compounds, appeared to be the all-purpose solution to any painting problem. Adding lead to paint increased its durability, because the tiny lead molecules carried the paint into pores and other irregularities of the surface being coated. In addition, various lead compounds enhanced colors, promoted drying, and had many other advantages.
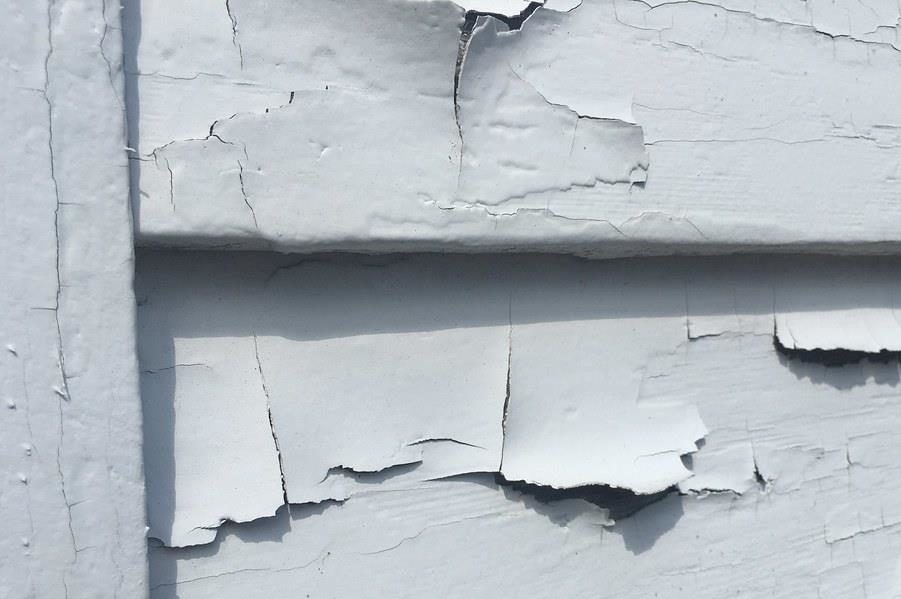
There was just one problem—lead is extremely poisonous. The most devastating effects are seen in children during the period of neurological development. Many health authorities consider the ages of six months to six years to be the most critical. Six months is the average age at which children become mobile. In addition to crawling, they engage in a lot of hand-to-mouth activity, which can result in the ingestion of lead dust. Very small amounts of lead (three granules of lead dust) can poison a child. Lead poisoning can cause irreversible IQ loss, and behavioral, hearing, and coordination problems. Although children under age six are most vulnerable, lead poisoning can cause damage at any age. Individuals exposed at any time in their lives may develop hypertension, anemia, kidney damage, or neurological damage. Women may experience pregnancy-related problems, including low birth weights and even miscarriage.
Many developed countries restricted or banned LBP for residential purposes beginning in the mid- to late 1800s. The United States, however, did not ban LBP for residential use until 1978 and approximately 38 million pre-1978 U.S. dwellings contain lead-based paint. The U.S. Centers for Disease Control and Prevention (CDC) estimates that almost a quarter of a million children aged 1-5 have blood lead levels greater than 10 micrograms of lead per deciliter of blood, the level at which CDC recommends public health actions be initiated. The good news is that number is a fraction of what it was in the early 1990’s, thanks to federal, state, local and industry efforts to reduce lead exposure, such as the ban on lead in paint and gasoline. However, there is no safe level of lead exposure and lead paint poisoning affects over one million children today.
U.S. Response
Perhaps the first determined effort to deal with this issue was the Lead-Based Paint Hazard Reduction Act of 1992. This legislation mandated federal agencies, including EPA, the U.S. Department of Housing and Urban Development (HUD), the Consumer Products Safety Commission (CPSC), and the Occupational Safety and Health Administration (OSHA), to develop guidelines for dealing with LBP.
EPA’s actions to implement the 1992 statute first focused on the lead abatement program, including developing the training and certification program for the identification and abatement of lead hazards (i.e., lead in dust and soil that exceeded federal hazard standards and lead paint in poor condition or on friction surfaces), the real estate disclosure requirements and developing the regulatory hazard standards. The Agency also authorizes states to administer the lead abatement program and, in those states where the program is not authorized, administers the lead abatement program directly. EPA also oversees the National Lead Laboratory Accreditation Program.
The 1992 law also directed EPA to promulgate regulations to ensure that those who perform lead-based paint activities, including renovation or remodeling activities that create lead-based paint hazards, are properly trained in lead-safe work practices through accredited training programs and that contractors performing these activities are certified by EPA or a state approved by EPA to administer its own lead program.
In 1995, HUD published the Guidelines for the Evaluation and Control of Lead-Based Paint Hazards in Housing, which established policies for working on federally assisted pre-1978 housing. The HUD Guidelines became the basis of HUD’s Lead-Safe Housing rule. Subsequently, many states adopted all or portions of the HUD Guidelines as the basis for their state codes concerning LBP.
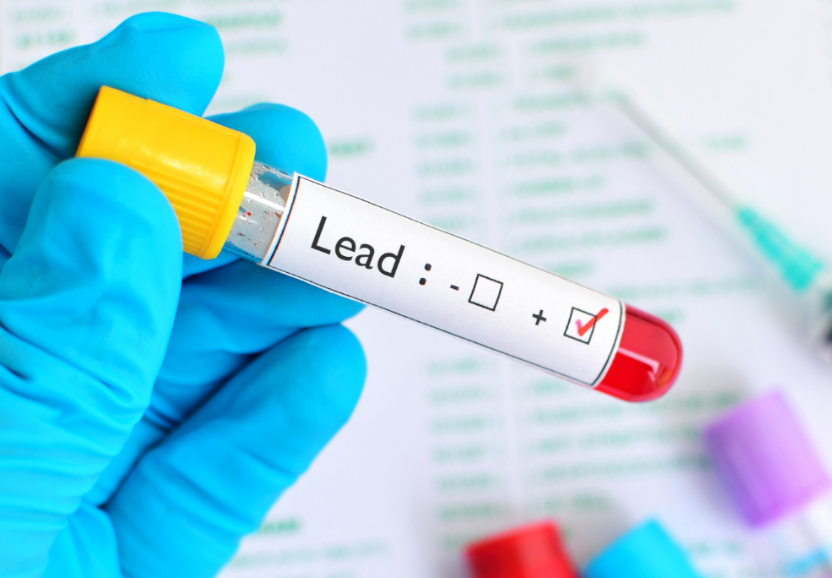
In 1993, OSHA developed the “Lead in Construction” standard (CFR 1926.62), which codifies health and safety requirements for lead exposure in the workplace. These requirements are based on levels of airborne lead dust, which are categorized as follows. Category 1 range is 30 micrograms per cubic meter (mcg/m3) or less. At that level, OSHA requires employee training, exposure monitoring, and record keeping. Category 2 range is 30–50 mcg/m3. At that level, OSHA requirements include all the provisions of category 1 plus the availability of respirators at employee request, exposure monitoring on a quarterly basis, and blood lead monitoring. Category 3 range is 50 mcg/m3. At that level, in addition to all the provisions of categories 1 and 2, OSHA requires respirator use, and the use of personal protective equipment (PPE) during all phases of lead exposure. OSHA also requires enforcement of housekeeping and hygiene practices. On-site cleaning facilities must be provided.
These levels can only be determined through air monitoring by a qualified person. In the absence of air monitoring, OSHA states that workers must operate under category 3 rules. OSHA highly recommends air monitoring, as PPE can become quite uncomfortable in hot weather.
EPA issued the Lead Renovation, Repair and Painting Program (RRP) rule in 2008 and the rule went into full effect on April 22, 2010. With the issuance of the 2008 Lead Renovation, Repair and Painting (RRP) rule, renovation firms working in pre-1978 housing or child-occupied facilities are required to be certified by EPA or a state program that has been approved by EPA and firms must use “certified renovators” for certain key aspects of the renovation job. Individuals who wish to become certified renovators are required to be trained by an EPA-accredited training provider in lead-safe work practices. The rule also strengthened and expanded existing lead-hazard information distribution requirements and prohibited certain dangerous work practices. At this writing, nine states have assumed responsibility for administering and enforcing the law. EPA administers the program in the other 41 states.
What You Need to Work Safely
Working lead safe requires some materials and equipment that might not otherwise be taken to the jobsite. These items serve to reduce the amount of lead dust created, to contain lead dust that is created, and to help leave a clean site after the work is completed.
Disposable ground cover is a necessity for both interior and exterior work. For interior work, most contractors prefer to use 6-mil plastic. Not only does ground cover capture any dust generated, but it makes cleanup much easier.
Six-mil is also useful when a vertical containment is required. The 6-mil can be attached to painter’s poles, or to other systems, such as ZipWall. The RRP rule establishes a minimum work area size of six feet from all painted surfaces that are disturbed, or the distance necessary to contain the dust and debris, whichever is greater. Impermeable, floor-to-ceiling vertical barriers may be used to limit the size of the work area below this 6-foot minimum.
Exterior plastic can be ordered in rolls of different widths and lengths. RRP rules call for minimum coverage of 10 feet from the base of the house when possible. Twelve-foot-wide exterior plastic allows that coverage with an adequate lap up the side of the wall in most instances. The standard the contractor must meet is that no dust or debris can leave the work area. The contractor must use at least 10 feet of plastic, but may require additional plastic on the ground or vertically to meet the standard.
Six-mil plastic is available at home improvement and hardware stores. Plants, including grass, are likely to be damaged by 6-mil plastic. A swath of burned-out grass around a home is not good advertising for your business, even if the lead-safe work was done in an expert manner! Typical landscaping fabric is not acceptable because it is not impermeable.
Spray bottles and pump sprayers are necessary to work wet when disturbing LBP. The idea is to apply enough moisture to cause chips and dust to drop quickly without dispersing. The proper amount of spraying should create a surface similar to morning dew. Overuse of water will create runoff and other problems. Water used in this manner is very effective on both interior and exterior applications. Another low-tech dust-control measure involves the use of shaving cream when drilling. A dab of shaving cream applied to the area to be drilled effectively contains dust and debris generated during the drilling process. Wiping the residue with a paper towel effectively eliminates the hazard. Ground cover is still needed to capture any residual dust.
HEPA vacuums are essential to safely vacuum leaded dust. A high-efficiency particle air (HEPA) filter is engineered to capture and hold the smallest (0.3 micron) lead particles. Shop vacs or household vacuums with a HEPA filter are not adequate for this purpose. The dedicated HEPA vacuum is a totally sealed unit that is engineered to capture all dust without any leakage. Also available are shrouded power tools that attach to HEPA vacs and allow virtually dust-free sanding, sawing, and cutting. Versatile drill shrouds are also available but may be harder to find. Commercial- or industrial-grade HEPA vacs and HEPA-shrouded tools may be special ordered from hardware stores or purchased online from companies that market dust-free tools.
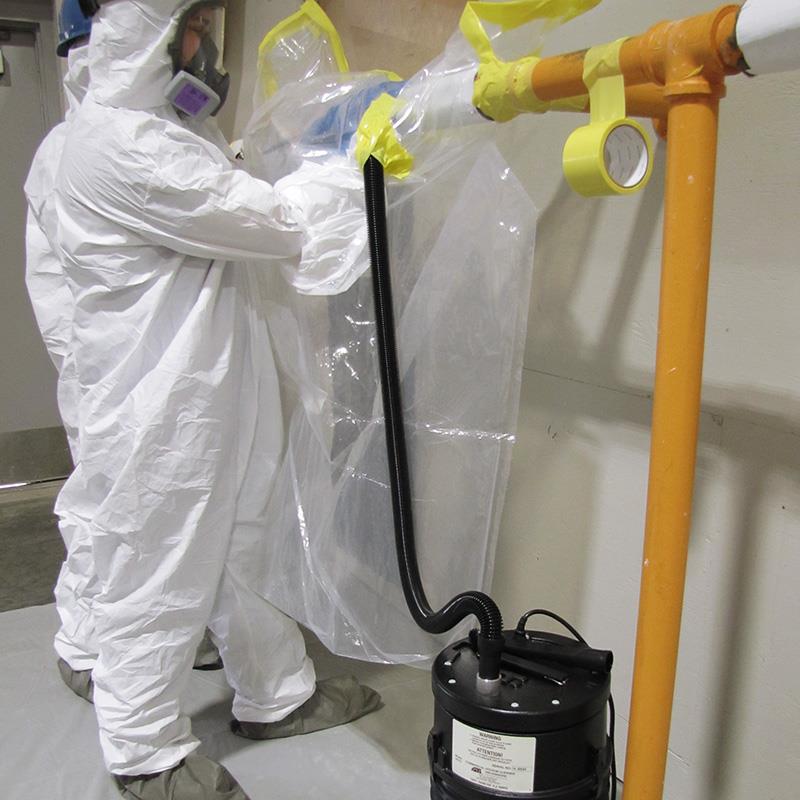
A variety of tapes are necessary for attaching ground cover to floors, walls, and other surfaces. Duct tape works well to join two lengths of 6-mil or to secure a length of 6-mil to a pole. Painter’s tape is the best option when attaching anything to painted or finished surfaces. Duct tape may damage paint or leave an unsightly adhesive residue that is difficult to remove. Tapes are available at home improvement, paint, or hardware stores.
Barriers such as caution tape, cones, signs, or rope serve to keep unauthorized people safely away from the work zone. RRP regulations state that a 20-foot distance from an exterior work area shall be maintained whenever space allows. Exterior renovations and entryways into an interior work area should be posted with signs prohibiting entry to anyone not associated with the job. Warning signs should state, “No eating, drinking, or smoking in the work area.” This precaution will help reduce lead poisoning resulting from hand-to-mouth ingestion of lead dust. These signs and barriers shall remain in place until cleaning verification or clearance testing has been completed.
RRP requires persons, tools, waste, and other items leaving the work area to be free of dust and debris. Foot covers and sticky mats help to ensure that lead-contaminated dust is not tracked out of the work area—HEPA-vacuuming or wet-wiping are other ways to do this. The shoe covers have an additional advantage in that the entire shoe surface stays cleaner during work. Sticky mats are widely marketed, and shoe coverings are available through hardware stores or from companies specializing in PPE.
In addition to these materials and equipment, working lead safe requires protective clothing. EPA recommends, but does not require, PPE. OSHA may require PPE in certain situations. People performing category 1 lead tasks should be provided with the following PPE:
- Coveralls may be disposable or washable. Washable coveralls should always be washed separately from any other family clothing. Disposable coveralls are widely available at home improvement, paint, and hardware stores.
- Respirators may be of the disposable N-100 type, or the reusable half-face negative-pressure type. Employers and workers who use respirators must follow OSHA regulations concerning medical evaluation, fit testing, and so forth before beginning use. OSHA regulations vary with the locality; check your local OSHA authority to determine the regulations for your area. Respirators are widely available in hardware stores and paint stores.
- Disposable gloves of latex, rubber, or plastic help keep lead-contaminated dust off workers’ hands. Most lead poisoning in children and adults comes from hand-to-mouth contact, so a barrier between the hands and potentially lead-contaminated surfaces helps to reduce the ingestion of leaded dust.
Cleaning Up
Workers should keep themselves and their tools as clean as possible. Lead dust is difficult to remove from surfaces, including hands and faces. Before eating, drinking, smoking, or applying lip balm or makeup, workers should wash their hands and faces thoroughly with soap and water and they should wash again before they leave the work site. Hand and power tools used in lead-sensitive work should be wiped down with a good-quality wet wipe before they are taken off the work site. This will prevent lead dust from being spread from one site to another.
After work has been completed, the work site must be cleaned to conform to one of two standards. The first is the standard specified by the EPA-RRP cleaning verification (CV) process. The second is the standard specified by HUD called a clearance examination. The CV is performed by the certified lead renovator on the jobsite, and is based on visual observation. The clearance examination is performed by a third-party certified or licensed lead inspector or risk assessor. This person collects dust-wipe samples, which are then analyzed for lead dust content by a laboratory certified by the National Lead Laboratory Accreditation Program (NLLAP). The CV and the clearance examination are described at greater length below.
In any case, there shall be no visible debris left in the work area. In general, cleaning involves using a HEPA vacuum on all surfaces inside the work area, followed by a detergent wash and clean-water rinse. Some contractors use a two-bucket system, with a mop, a wringer, one bucket of cleaning solution, and one bucket of rinse water. Others use a wet-jet cleaner such as a Swiffer system. One advantage of using a wet-jet system is that it is much easier to see when the pad is getting dirty, as compared to a mop head. Another advantage of the wet-jet system is that there is less lead-contaminated water to dispose of.
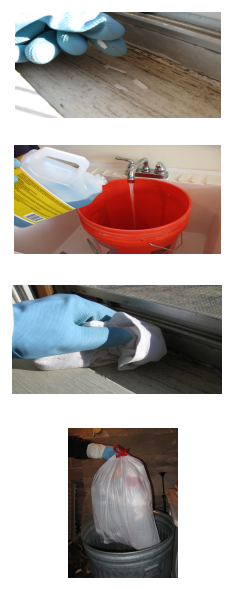
Incidentally, lead-contaminated wastewater may be flushed down a toilet, as long as there is a municipal waste-treatment system. In areas where septic systems are used, any wastewater must be transported to an area where there is a wastewater treatment plant. This is not an RRP rule, and there may be state or local requirements that govern wastewater.
Cleaning verification is one way to determine whether a job site is clean enough after work has been completed. Cleaning verification was developed by EPA as part of the RRP rule. Verification must be done on floors, countertops, and windowsills. This procedure involves wiping down a cleaned area with a white, moist, disposable cloth. This cloth is then compared to a sample on an EPA cleaning verification card. The cloth should appear to be no dirtier than the sample on the verification card.
Clearance testing is required on any job that is financed by HUD. Many states and localities have other laws requiring the use of clearance testing in certain situations. Clearance testing is done by a certified or licensed professional. Dust wipe samples are taken using an approved wipe medium and an approved sampling medium. The wipe samples are then sent to an NLLAP lab for analysis, as described above. Areas tested for clearance are floors, windowsills, and window troughs. HUD and EPA health-based standards are the threshold clearance levels.
There has been much discussion concerning the added time and cost associated with lead-safe renovation or lead-abatement projects. One study looked at the total time and materials costs associated with lead-safe rehabilitation versus standard practice. The authors of this study found a 15%–25% increase in job costs associated with lead-safe rehabilitation.
Lead-safe work does require the use of materials that may not have been used in the past, and in general requires more attention to detail and cleanup than some contractors may have practiced previously. This work calls for thorough preparation and the assurance that all needed materials are on the jobsite.
Learn to Work Lead Safe
Complying with these policies and procedures may seem daunting to someone who has never worked lead safe before. There is a learning curve involved, and many of us need to be able to change our work habits to become comfortable with these procedures. Most people are able to adapt in a short time and see the benefits of working lead safe. People usually find that proper preparation leads to easier and quicker cleanup. Customers are happier, and workers are happier knowing that they are not working in a dangerous environment, nor are they carrying poisonous lead dust home to their families.
To learn more, visit www.epa.gov/lead.
Earn CEUs
Earning CEUs on the BPA Journal is a member-exclusive benefit. Please log in to complete the quiz and earn them or join as a member today.